Основи на рязане на метал: инвертор, плазма, газ. Рязане с кислород-пропан.
Рязане с кислород - процесът на изгаряне на метали и техните сплави в потока технически чист кислород. За тази цел, металът по протежение на линията на предвиденото сечение се нагрява до температурата на запалване в кислорода. По този начин целият процес може да бъде разделен на етап на нагряване с ацетиленов пламък (или пламък от други газове) и етап на рязане на метал с кислородна струя, по време на която металът се изгаря и образуваните оксиди се издухват от участъка на разреза. Това рязане е друго име - разделяне (Фиг. 124). Предназначен е за рязане на метални листове, режещи ръбове за заваряване, рязане на заготовки с различни форми и други работи, свързани с рязане на метал на парчета. Описаното по-горе рязане може да се използва и за рязане на канали, отстраняване на повърхностния слой от метал и отстраняване на повърхностни дефекти. В този случай рязането ще се нарича повърхност (фиг. 125).
Фиг. 124.
Фиг. 125.
Класификационни фрези и инсталации за ръчно рязане
Инструмент като кислород, удобно комбинира всички етапи на рязане и е предназначен за правилно смесване на горими газове или течни пари с кислород, образуване на нагряващ пламък и подаване на струя чист кислород към зоната на рязане. Резачките се класифицират по принципа на смесване на газ (инжектиране и неинжектиране), по предназначение (универсален, щепселен и специален), чрез приложение (за ръчно и машинно рязане) и по вид нарязване (за сепариране и повърхностно рязане). Понастоящем широко се използват универсални инжекторни ръчни горелки за разделно рязане, чиято структура е показана на Фигура 126. \\ t
Фиг. 126:
1, 2 - нипели, 3, 4 - кислородни тръби, 5 - външен мундщук, 6 - инжектор, 7 - смесителна камера, 8 - вътрешен мундщук
Като образец бе взет средностабител Р2А-01, използван за ръчно рязане на нисковъглеродна и нисколегирана стомана с дебелина до 200 мм. Принципът на работа на горелката е следният. Ацетиленът се подава през маркуч към зърното 1, а кислородът се подава към зърното 2. От зърното 2 кислородът отива в две посоки. Една част от кислорода, както при конвенционалните заваръчни горелки, влиза в инжектора 6, а след това в смесителната камера 7. При последната се образува запалима смес от кислород с ацетилен, която влиза през зърното 1. След това сместа минава през тръбата, преминава през пръстеновидната междина между външната 5 и вътрешни 8 мундщуци и образува нагряващ пламък. Останалата част от кислорода през тръбите 3 и 4 се придвижва към централния отвор на вътрешния мундщук 8 и създава струя за рязане на кислород.
В малки работилници сега се използват специални, универсални и щепселни фрези с ниска, средна и висока мощност. Специални ножове от марки RPA-2-72, RPK-2-72, RZR-2, RK-02 могат да режат метал с дебелина от 200 до 800 мм. Ножът RZR-2 с тегло 5,5 кг като горивен газ използва смес от пропан-бутан, чиято максимална консумация е 7,5 м3 / ч. Най-високата консумация на кислород е 114,5 m3 / h. Инструментът има дюза за смесване на кислород и запалим газ. Налягането на запалим газ на входа на ножа е не по-малко от 0,05 MPa (0,5 kgf / cm2) и има манометър за контролиране на кислородното налягане. Потокът от запалим газ идва от разпределителните рампи или от главния магазин. Ако се използва линия, тогава трябва да имате релса за пропан-бутан за 3 цилиндъра и кислородна релса за 10 цилиндъра. RZR-2 се използва за рязане на печалби, изковки и отливки от нисковъглеродни и нисколегирани стомани; може да отреже метал с дебелина до 800 мм.
Фреза PK-02 или керосин има изпарител, нагряван от нагряващ пламък. Като гориво се използва бензин или керосин (или тяхната смес). Това гориво идва от сферичен резервоар BG-02 с обем 8 литра при налягане 0,3 MPa (3 kgf / cm3). Резервоарът има предпазен клапан и ръчна помпа. Руската промишленост RK-02 се произвежда под формата на комплект от КЖГ-1 заедно с резервоар BG-02 за рязане с използване само на течно гориво. Инструментът е предназначен за ръчно разделно рязане на метален скрап, ламарина, релси и скрап с дебелина до 200 мм.
Ножовете RPK-2-72 и RPA-2-72 с маса 2,5 кг и дължина 13,5 см са снабдени с корпус с вътрешни и външни мундщуци, лост за стартиране на кислород за рязане и няколко клапана. За да се получи широка и мека струя за рязане на кислород, диаметрите на изходните канали в мундщуците и поточните секции са малко по-големи, отколкото при универсалните горелки. Универсалните фрези Р2А-01 и РЗП-01, съответно със средна и висока мощност, имат доста големи диаметри на каналите на мундщука, смесителната камера и инжектора. Фреза P2A-01 включва използването на ацетилен, а ножът RZP-01 - бутан, пропан и природен газ.
Ръчни ножове
Устройството UVR-5 е предназначено за прахово-кислородно рязане на стоманобетон с дебелина до 300 мм и работи с пропан или бутан, смесен с кислород. Устройството включва носител за флюс на количка, нож, държач за цилиндри и държач за копие, предназначен да фиксира тръбата, през която влиза кислород. Flux е смес от два прахове: желязо (75-85%) и алуминий (15-25%); освен това, въздухът се използва като газ, пренасящ потока. Дълбочината на отвора, изгорен в стоманобетон UFR-5, може да бъде 1.5 m.
Въртящото оборудване на ASSh (“Spark”) и ASSH-B за кислородно рязане има пантограф, който ви позволява да направите фигурно рязане едновременно с три малки части с дебелина на материала от 5 до 100 mm при скорост на рязане до 1600 mm / min. Масата на тези растения е около 350 кг и те осигуряват първия клас на точност, когато се използва само един факел.
127. :
а - изглед отпред, б - изглед отстрани; 1 - количка, 2 - циклон, 3 - подаващ механизъм, 4 - кислороден редуктор, 5 - нож, 6 - маркучи
Инсталацията на UGPR е сходна по дизайн с UFR-5, но има някои особености. Инсталацията има универсален нож Р2А-01 в блок с механизъм за подаване на флюс, както и резервоар за подаване на флюс с скоростна кутия DKS-66, които са фиксирани на количка (фиг. 127). Желязният прах PZh, който се продухва с кислород, се използва като поток. Трябва да се отбележи, че UGPR е монтиран на базата на инсталациите URHS-5 и URHS-6.
Освен посочените инсталации, има и преносими машини за кислородно рязане - Gugark, Orbita-2 и Sputnik-3. Тези машини са самоходни колички, движещи се по разрязания метал и оборудвани с нож. Последната инсталация с тегло 18 кг е предназначена за рязане на стоманени тръби с диаметър от 190 до 1620 мм с дебелина на стената от 5 до 75 мм при скорост 100-900 мм / мин.
Рязане с кислород
Трябва незабавно да се отбележи, че само метали, които отговарят на следните основни изисквания, могат да бъдат подложени на рязане. Точката на топене на метала трябва да бъде по-голяма от температурата на запалване в кислорода. В противен случай металът ще се стопи, но няма да гори. Например, нисковъглеродната стомана има температура на запалване в кислород от 1300-1350 ° С и нейната точка на топене е около 1500 ° С. Въпреки това, увеличаването на количеството въглерод в стоманата ще бъде придружено от повишаване на температурата на запалване в кислорода и намаляване на температурата на топене. В тази връзка рязането на стомана с високо съдържание на въглерод и примеси става проблематично.
Точката на топене на метала трябва да бъде по-висока от точката на топене на оксидите. Това изискване е необходимо, така че оксидите, образувани по време на рязане, да бъдат лесно издухани от кислород и да не пречат на по-нататъшно окисление и рязане. Например, при рязане на алуминий се образуват оксиди с точка на топене приблизително 2050 ° С и при рязане на хромови стомани, оксиди с точка на топене от около 2000 ° С. Очевидно е, че тези оксиди покриват повърхността на метала и по този начин прекратяват следващия процес на рязане.
Топлинната проводимост на метала трябва да бъде колкото е възможно по-ниска, тъй като с висока топлопроводимост топлината, предавана на метала, бързо напуска зоната за рязане и ще бъде трудно да се нагрее такъв метал до температурата на запалване.
Количеството топлина, отделяно по време на горенето на метала, трябва да бъде достатъчно голямо, тъй като тази топлина загрява металните зони, граничещи със зоната на рязане и по този начин осигурява непрекъснатостта на процеса на рязане. Така например, при рязане на нисковъглеродна стомана, 65-70% от общото количество топлина се освобождава от изгарянето на метала в кислородната струя, а останалите 30-35% е топлината от нагряващия пламък на режещия апарат.
Получените по време на рязане шлаки трябва да бъдат достатъчно течни и лесно да се издухат от разреза. Вискозните и огнеупорни шлаки сериозно ще затруднят процеса на рязане. Преди рязане внимателно почистете повърхността на метала, който се изрязва от ръжда, скала, мръсотия и боя. За да ги отстраните, е необходимо бавно да държите пламъка на горелката върху металната повърхност по желаната линия на рязане. В този случай скалата изостава от метала, а боята и маслото изгасват. След това трябва да почистите металната повърхност с четка.
Трябва да се отбележи, че различни метали в различна степен са подложени на кислородно рязане. Много добре се нарязват нисковъглеродни стомани с въглеродно съдържание от не повече от 0,3%, докато средновъглеродните стомани (с количество въглерод не повече от 0,7%) са малко по-лоши. Високовъглеродните стомани се изрязват с голяма трудност и при съдържание на въглерод над 1%, рязането е невъзможно без добавянето на специални потоци. Високолегираните стомани не могат да бъдат заварени към кислородния газ, за тяхното рязане трябва да се използват плазмени дъгови или кислородни потоци, които също могат да бъдат нарязани на мед, месинг и бронз. За рязане на алуминий и неговите сплави приложими рязане с плазмена дъга, По този начин, след характеристиките на разрезимостта, е необходимо да се изследват особеностите на технологията за рязане на различни метали в зависимост от тяхната дебелина, вида на профила, който се реже, химическия състав и деформируемостта в резултат на високотемпературна експозиция.
Ако дебелината на метала не достигне 300 mm, тогава е достатъчен нормален пламък. При дебелина на метала над 400 mm дължината на пламъка на нагряващия пламък трябва да бъде увеличена поради излишния поток ацетилен. Това ще затопли метала дълбоко. Скоростта на рязане играе голяма роля в ефективността на работата. Скоростта на горелката трябва да съответства на скоростта на горене на метала. Най-лесният начин за определяне на скоростта ще бъде естеството на излъчване на искри и шлака (Фиг. 128).
Фиг. 128:
a - бавна скорост на рязане; b - нормална скорост на рязане; - бърза скорост на рязане
Ако скоростта на горелката е правилна, тогава потокът от искри и шлака се изважда от среза право надолу, а ръбовете са чисти, без увисване и топене. При ниски скорости потокът от искри е пред резачката, а ръбовете на среза се стопят и покриват със сода. При висока скорост снопът от искри изостава от режещия инструмент, а металът в долния край няма време да гори, така че чрез рязане спира.
Производителността на рязане зависи от правилното положение на ножа. Рязането на стоманена ламарина с дебелина до 50 мм е както следва. В самото начало на рязането, нагряващият пламък трябва да бъде насочен към края на отрязания метал, за да се загрее ръбът до температурата на претопяване. След това мундщукът на режещия инструмент трябва да бъде поставен перпендикулярно на повърхността на метала, който се реже, така че струята на нагряващия пламък и след това кислородът за рязане да лежи по вертикалния ръб на метала. След като металът се нагрее до температурата на запалване, трябва да се изстрелва поток от кислород. Необходимо е режещият механизъм да се движи само след като металът бъде прорязан през цялата му дебелина в самото начало на линията на рязане.
За да се предотврати закъснението при рязане в долните слоеве на метала, в края на процеса трябва да се направи ъгълът на наклон на режещия инструмент при 20-30 ° в посока, обратна на движението му, и да се намали скоростта на движение на инструмента.
Фиг. 129:
и - началото на рязане; б - процес на рязане
Фиг. 130.
Фиг. 131.
При работа с метал с по-голяма дебелина (100-200 mm), ъгълът на наклон трябва да се намали до 10-15 °. Предварителният загряване до 300-400 ° C ще позволи рязане с повишена скорост. Положението на фрезата по време на работа е показано на фигура 129. Ширината и чистотата на среза зависят от метода на рязане и дебелината на метала. Машинно рязане дава по-малка ширина на рязане и по-чисти ръбове, отколкото ръчно рязане, Колкото по-дебел е срязаният метал, толкова по-голяма е ширината на среза.
Ако се извършва рязане на заготовки с кръгло напречно сечение, тогава в началото на рязането трябва да се направи ъгъл на наклона на режещия инструмент, след което постепенно да се намали в процеса на работа до перпендикулярната позиция на режещия инструмент (фиг. 130). Трябва да се отбележи, че при изрязването на извитите части позицията на режещия елемент спрямо металната повърхност трябва да бъде строго перпендикулярна. Когато режете няколко метални листа, те трябва да бъдат фиксирани в торба, за да направят процеса продуктивен. Краищата на листата в началото на рязането трябва да се сгънат, както е показано на фигура 131.
Изгарянето на дупки има редица характеристики. Когато дебелината на метала е до 20 мм, първо трябва да се затопли до желаната температура, след това пламъка на отоплението трябва да се изключи и кислородът за рязане да се стартира чрез плавно отваряне на вентила на режещия инструмент. От горещия метален кислород се самовъзпламенява. Тази процедура помага да се предотврати обратния огън на пламъка. Когато дебелината на метала е 20-50 mm, листата или частта трябва да бъдат монтирани във вертикално или наклонено положение, така че образуването на шлака да се извърши незабавно. В този случай първоначалният отвор се пробива на малка дълбочина. Освен това, ходът на работа е същият като в предишния случай.
По време на работа мундщукът трябва да се държи на определено разстояние от металната повърхност. За да направите това, можете да използвате количка или други устройства, които са прикрепени към главата на ножа. При рязане на метал с дебелина до 100 мм, разстоянието между металната повърхност и края на мундщука трябва да бъде с 2-3 мм по-дълго от дължината на ядрото на пламъка. При рязане на метал с дебелина над 100 mm и при рязане на заместители на ацетилен, разстоянието трябва да се увеличи с 30-40%, за да се предотврати прегряването на мундщука. Броят на мундщука (вътрешен и външен) трябва да се избира в зависимост от дебелината на метала.
По този начин ръчното рязане може да бъде успешно само когато работникът спазва препоръчания ъгъл на наклон на режещия инструмент, точно определя мястото, където започва рязането, внимателно избира номера на мундщука и горимия газ.
Фиг. 132:
и - високоскоростно рязане; b - ролково рязане
Рязането на тръбите може да се извърши с помощта на ацетилен и неговите заместители. При рязане тръбата може да се върти с ролки, както е показано на фигура 132. Тази фигура показва правилното положение на режещия инструмент, при който зоната на взаимодействие между метал и кислород рязко се увеличава и образуваната по време на работа шлака загрява граничните зони на тръбата. Това от своя страна значително подобрява условията за рязане на метал. В същото време това положение на режещия механизъм удължава времето за предварително загряване на метала до температурата на запалване до 60-70 s. За да се скъси времето за нагряване, е необходимо незабавно да се въведе стоманена пръчка или железен прах в секцията за рязане. Тогава скоростта на рязане на тръби с дебелина на стената до 12 mm и диаметър 300-1020 mm ще бъде 1,5-2 m / min.
При рязане на отливки и изковки с дебелина 300-800 mm, можете да използвате ръчен факел тип RZR-2, който в началото на рязането трябва да бъде поставен перпендикулярно на повърхността, която се реже (или под ъгъл 5 ° в посока, обратна на движението). След това металът трябва да бъде прорязан в началото на линията на рязане след предварително загряване. След това трябва да започнете да движите инструмента под същия ъгъл и до края на среза трябва да направите ъгъл на наклона на инструмента от 10-15 ° към страната, противоположна на движението, и да намалите скоростта на движение. Това е необходимо за окончателното рязане на последния участък.
Деформация при рязане и борба с нея, Неравномерното нагряване и охлаждане на части или заготовки в процеса на рязане води до остатъчни напрежения в метала и деформация. За да избегнете това, трябва да следвате следните практически препоръки, когато работите:
- преди работа трябва да вземе почивка;
- винаги започвайте да режете с най-дългия край и завършете на късия ръб;
- първо изрязани малки части, а след това големи;
- скоростта на рязане трябва да бъде изключително висока, така че металните ръбове да не се загряват много;
- дупките за рязане трябва да се извършват преди друга работа;
- в процеса на работа за охлаждане на метала с вода;
- първо трябва да извършите зигзагообразни срезове, а след това направо;
- преди работа металните листове трябва да бъдат здраво закрепени, за да се предотврати тяхното изместване под въздействието на остатъчни напрежения;
- в присъствието на джъмперите те се елиминират след приключване на работата по рязане.
Ръчното рязане на метали с голяма дебелина (300-700 мм) се извършва с резачка тип RZR-2, която дава нагнетяващия пламък с необходимия размер. Инструментът в началото на рязането трябва да има наклон в посока на движение от 2-3 ° спрямо равнината на края, а в края на процеса - 2-3 ° в посока, обратна на посоката на движение (фиг. 133).
Фиг. 133:
и - преди рязане; b - преди края на рязането
Изрязване на флуида
Цветните метали и техните сплави, чугуните, неръждаемият хром и никел-хромните стомани не могат да бъдат отрязани чрез обичайно газо-кислородно рязане. За да направите това, използвайте плазмена дъга и по-добра рязане на кислородния поток. Същността на последното се състои в това, че праховият поток заедно с кислород за рязане непрекъснато се подава в зоната за рязане с помощта на специално оборудване. Потокът гори и разтопява огнеупорните оксиди. В допълнение, флюсът превръща оксидите в течна шлака, лесно тече от мястото на среза. Това рязане се използва главно за работа с чугун и високолегирани стомани с дебелина до 70 мм.
Флюсът използва фино гранулиран железен прах марка PZH5M (ГОСТ 9849-74) с размер на частиците от 0.07 до 0.16 mm (използван за рязане на желязо и мед). За рязане на неръждаеми стомани до посочения прах добавете 10-12% алуминиев прах APV. Можете да използвате алуминиево-магнезиев прах (60-80%) в смес с феросилиций (20-40%). При рязане на хромови и хром-никелови стомани се използва железен прах PZh5M с добавка на 25-50% скала. При рязане на желязо, можете да добавите 30-35% домен ферофосфор към този прах. При рязане на мед и неговите сплави се използва смес от железен прах с алуминиев прах (15-20%) и ферофосфор (10-15%).
Това рязане се извършва чрез инсталиране на URHS-5, състоящ се от фреза и подаващо устройство. Машината може да изрязва високолегирана хром-никелова и хромова стомана с дебелина 10–200 mm при скорост на рязане 230–760 mm / min ръчно или машинно. Консумацията на кислород на 1 m сечение е 0.20-2.75 m3, ацетилен - 0.017-0.130 m3 и флюс - 0.20-1.3 kg. Чугун с дебелина 50 mm се нарязва със скорост 70-100 mm / min с консумация на кислород 2-4 m3 на 1 m, 0,16-0,25 m3 ацетилен и 3,5-6 kg флюс. При рязане на медни сплави се получават приблизително същите параметри.
Трябва да се има предвид, че мощността на отоплителния пламък трябва да се увеличи с 15-25% в сравнение с конвенционалното газово рязане, тъй като определена част от топлината на този пламък ще отиде за нагряване на потока. Пламъкът трябва да бъде нормален или с лек излишък от ацетилен. От края на мундщука на горелката до металната повърхност трябва да има разстояние 15-25 мм. С малко разстояние са възможни удари и възпламенявания на пламъка, дължащи се на отскачането на частиците от потока от повърхността и тяхното попадане в дюзата на режещия инструмент. В допълнение, може да има прегряване на мундщука и следователно нарушение на процеса на рязане. Ъгълът на инструмента трябва да бъде направен 1-10 ° в посока, обратна на посоката на рязане. За да се улесни процесът на рязане, медните сплави трябва да бъдат предварително загряти до 200-50 ° C, а стоманите от хром и никел - до 300-400 ° C.
На практика рязането на бетон и стоманобетон се извършва доста често. Извършва се по два начина: кислородно-пистови и прахо-режещи. Киселинно копие рязане много добре изгаря дупки в бетона. Тя ви позволява да получите отвори до 4 м дълбочина с диаметър до 1,2 м. С това рязане можете успешно да изгорите дупки в стоманена заготовка. Този метод използва стоманена тръба (копие), единият край на която се загрява до температурата на претопяване и се прикрепя към бетонната повърхност. Кислородът се продухва през копието, което, взаимодействащо с горещия край на тръбата, се възстановява. Когато това се случи, течните железни оксиди, които реагират с бетона и се превръщат в шлаки, които след това лесно се издухват. Като движите тръбата напред, можете да изгорите необходимия отвор в бетона.
Като копие можете да използвате газова тънкостенна тръба с диаметър 10-20 мм, запълнена със стоманени пръти за 60-65% от обема си или обвита отвън със стоманена тел с диаметър 3-4 мм, както и безшевна дебелостенна тръба с диаметър 20-35 мм. При такъв разрез жицата и прътите изпълняват същата функция като потока при рязане на кислородния поток. Копието се загрява, като правило, с въглероден електрод или горелка.
Нарязването на прах и копие се характеризира с факта, че използва желязо-алуминиев прах в съотношение 85: 25. Подобно на флюс, този прах се продухва от потока кислород в зоната на рязане. Параметрите на извършената работа в този случай могат да бъдат както следва. Например, при изгаряне на отвор с диаметър 50 mm и дълбочина 500 mm, скоростта на аванс ще бъде 120-160 mm / min с кислородно налягане от 0,7 MPa, разход на прах от 30 kg / h и потребление на копие (тръба) от 4 mm на всеки метър дължина. дупки. При дълбочина на отвора от 1,5 m и същия диаметър, скоростта на драгиране ще намалее до 40–70 mm / min с кислородно налягане от 1,0–1,2 MPa, разход на флюс от 30 kg / h и разход на копие от 6 mm на 1 m дължина на отвора.
Повърхностното рязане е вид кислородно рязане. Тя е предназначена да отрязва релефа върху металната повърхност под формата на един или няколко отделни или подравнени вдлъбнатини. При заваряването това рязане често се използва за рязане на дефектни фуги. С това рязане, източникът на нагряване на метала ще бъде както пламъкът на ножа, така и разтопената шлака, която по време на разпръскването си загрява дълбоко лежащите слоеве от метал. Горелките RPA и RPK са подходящи за този вид работа. Режимът на рязане и ъгълът на инструмента играят важна роля в ефективността на повърхностното рязане.
В началния етап е необходимо да се затопли зоната на рязане до температурата на запалване. Резачът трябва да бъде поставен под ъгъл 70-80 ° спрямо металната повърхност. Преди подаване на кислород за рязане, инструментът трябва да бъде наклонен под ъгъл от 15-45 °. В процеса на рязане възниква фокално изгаряне на метала; това осигурява ефективно почистване на металната повърхност, включително поради равномерното движение на инструмента по линията на планираното рязане. Положението на фрезата при този вид рязане е показано подробно на фигура 134.
Фиг. 134:
1 - мундщук; 2 - шлака; 3 - жлеб
Ширината и дълбочината на жлеба намаляват с увеличаване на скоростта на рязане. В допълнение, дълбочината на канала се намалява, когато ъгълът на наклона на устната на инструмента намалява и когато налягането на кислородът за рязане падне. Ширината на канала зависи от диаметъра на струята кислород. По време на рязане на повърхността е необходимо да се направи ширина на браздата 5-6 пъти по-голяма от дълбочината, за да се предотврати появата на залези на повърхността. Ако е необходимо да се изчистят многобройни дефекти върху голяма площ, тогава в този случай е необходимо да се отреже „рибена кост” в един или няколко преминавания, като се използват колебателни движения на ножа.
Характеристики на въздушно-дъговото рязане
Аеродинамичното рязане е един от видовете сепарационно рязане и се основава на топенето на метал от зоната на рязане чрез топлината на електрическа дъга, възбудена между отрязания метал и електрода. Когато този поток сгъстен въздух непрекъснато премахва разтопения метал от кухината на разреза. Този вид нарязване е намерен широко приложение по време на строителни и монтажни работи за грубо рязане на метал с дебелина до 30 мм, но само ако не се нуждаете от високо качество, тъй като ширината на рязането ще бъде 2-3 пъти по-широка, отколкото при рязане с кислород. Това рязане се извършва и за топене на дефектни фуги, елиминиране на врати, обработка на отливки и почистване на повърхности. Скоростта на такова рязане с дебелина на метала от 15 mm не надвишава 120-150 mm / min. Консумацията на електрода е 1,0-1,5 kg на 1 m от отрязания метал. Диаграма на устройството за рязане за рязане с въздушна дъга Фигура 135. Тя има клапан за пускане на въздух и дюза за подаване на сгъстен въздух към секцията за рязане. Ток и въздушен поток през комбинирания кабелен маркуч.
Фиг. 135:
1 - тръба за подаване на въздух; 2 - захранване с електродна тел; - тяло на ножа; 4 - дъга; 5 - дюза за сгъстен въздух към зоната на горене; 6 - празна проба; 7 - разтопена част от детайла
Електроди за въздушно-дъгово рязане са представени под формата на въглеродни, графитни, графитизирани цилиндрични пръти или плочи с дължина от 250 до 350 mm. Медните електроди са много по-добри от други, тъй като са по-малко податливи на окисление. В момента в практиката са широко използвани 2 вида фрези: RVDm-315 и RVDl-1200. Първото устройство е проектирано за ток от 315 А, а въздушният поток е 20 м3 / ч. RVDm-315 има маса от 0,8 кг и широк спектър от приложения. Диаметърът на електрода в този апарат е 6-10 mm. RVDl-1200 използва ток от 1200 A при дебит на въздуха от 35 m3 / h. Това устройство може да коригира отливки, използвайки електроди с диаметър най-малко 15-25 мм. Масата на устройството е 1,6 кг. Въздухът е под налягане 0,4-0,6 МРа или от компресор с капацитет 20-30 м3 / ч или повече, или от въздушна линия. В същото време е необходимо да се използват маслоотделители, тъй като въздухът трябва да е чист.
За този вид рязане можете да използвате както пряк, така и променлив ток. По източници постоянен ток могат да се използват заваръчни преобразуватели или единични и мулти-изправители. Като източници на променлив ток могат да се използват трансформатори с ниско напрежение и точни характеристики на токовото напрежение. празен.
Безопасност по време на газово заваряване и операции по газовото рязане
При тези видове работа са възможни следните видове наранявания: токов удар, изгаряния от метални и шлакови капки, увреждане на очите и повърхността на кожата от електрически дъгови лъчи, натъртвания и наранявания от експлозии на цилиндри на сгъстен газ и заваръчни съдове от запалими вещества, отравяне с вредни газове , прах и изпарения, отделени при заваряване. За да се предпазите от електрически удар, трябва да се спазват следните условия.
Загражденията за източници на електроенергия от дъга, заварените продукти и заваръчното спомагателно оборудване трябва да бъдат надеждно заземени медна жицаединият край на който е закрепен или към метален прът, закрепен в земята или към обща заземителна повърхност, а другият край е прикрепен към тялото на енергийния източник на дъгата, а именно към специален болт с надпис "Земя".
Заземяването на преносимите източници на захранване се извършва, докато се включи в електрическата мрежа, а заземяването се премахва само след изключване от мрежата. Свързване на източници заваръчен ток към мрежата е задължително използване на стенни кутии с ножови превключватели, скоби и предпазители. Дължината на захранващите проводници не трябва да надвишава 10 м. Тел трябва да бъде окачен на височина 2,5-3 м. Входовете и изходите трябва да бъдат оборудвани с фунии или втулки, които предпазват жиците от огъване, а изолацията - от повреда. Свържете и изключете електрическото заваръчна техника, както и да следят доброто им състояние по време на работа изискваха електротехници. Заварчици такава работа е забранена.
Не използвайте проводници с повредена и стара изолация. Изолацията трябва да съответства на силата на прилагания ток. По време на работа на открито заваръчното оборудване трябва да е под навес, за да се предпази от сняг и дъжд. При отсъствие на тези условия не се допуска заваряване. Не забравяйте да използвате гумена подложка, галоши и гумена каска, както и подложки и подлакътници, подгънати с филц, при заваряване на вътрешни шевове на котли, тръби, резервоари и други затворени и дори по-сложни структури. Всички електрически заваръчни съоръжения трябва да бъдат оборудвани с устройства (ASN-1, ASN-30 или AST-500), за да се изключи автоматично напрежението в отворената верига или да се ограничи до безопасна стойност.
Ако възникне токов удар, жертвата трябва да бъде подпомогната: първо, освободете го от електрическите проводници, осигурете свеж въздух, и ако е в безсъзнание, възможно най-скоро направете изкуствено дишане и повикайте линейка. За защита от пръски от метал и шлака трябва да се използва гащеризон, а лицето да се покрие с щит, маска или каска. Трябва да се отбележи, че при заваряване на хоризонтални, таванни и вертикални шевове, трябва да се носят платна и да се връзват здраво върху ръкавите. Комбинезоните на заварчика се състоят от платнен костюм, платнени ръкавици и кожени или филцови обувки. Панталоните трябва да са без маншети, гладки, да се спускат върху ботуши или ботуши. Ръкавите трябва да се обличат с ръкави и да се завържат с плитка.
За да предпазите очите и кожата от излъчването на електрическа дъга, трябва да използвате и маска, щит или каска, тъй като яркостта на светлинните лъчи значително надвишава нормата за човешкото око и произвежда ослепителен ефект. Излъчването на невидими ултравиолетови лъчи при изгаряне на заваръчна дъга може да причини очно заболяване, наречено електрофтальмия в продължение на няколко секунди, което се характеризира с остра болка, разкъсване, спазми на клепачите и резу в очите. От тези лъчи върху кожата с продължително излагане може да изгори. Инфрачервеният спектър на излъчване по време на изгаряне може да причини замъгляване на очната леща (катаракта) и изгаряния на лицето. Въпреки това, тези защитни средства имат отвор за гледане, снабден със светлинен филтър, който намалява яркостта на светлинните лъчи на дъгата и освен това предотвратява инфрачервените и ултравиолетовите лъчи. Отвън, за да се предпази от пръскане, металният филтър е защитен от просто прозрачно стъкло.
Предотвратете опасността от експлозия. При неправилно съхранение, транспортиране и използване на цилиндри със сгъстен газ, както и по време на заваръчни операции в различни контейнери може да възникне експлозия, без първо да се почистят от остатъци от запалими вещества. Строго е забранено да се монтират цилиндри в близост до отоплителни уреди или под слънчева светлина. Цилиндрите на работното място трябва да бъдат добре закрепени в изправено положение, като се елиминира възможността за натъртвания и падания. В никакъв случай не може да се затопли с открит пламък редукторът на цилиндър с въглероден диоксид и във всички цилиндри със сгъстен газ. Затоплянето може да се извършва само с парцали, напоени с гореща вода.
Трябва да се разреши използването само на одобрени и годни за експлоатация цилиндри. Транспортирането на бутилките може да се извършва на специални носилки или на пружиниращи колички. За да направят това, те завинтват защитните капачки на цилиндрите и ги поставят върху дървени облицовки с тапицирани с филц контакти. Винаги трябва да се помни, че съвместното транспортиране на кислородни и ацетиленови бутилки е забранено.
По време на работа цилиндърът се фиксира във вертикално положение със скоба на разстояние най-малко 5 m от точката на заваряване. Преди да започнете работа, изходът на цилиндъра трябва да се прочисти. Потреблението на газ трябва да се извършва до остатъчно налягане на кислорода не по-малко от 0,05 MPa и ацетилен 0,05-0,1 MPa. След приключване на работата внимателно затворете клапана на бутилката, освободете газа от редуктора и маркучите, след това свалете редуктора, фиксирайте капачката на дюзата и завийте капачката на вентила. Необходимо е също така своевременно да се изследват бутилките (веднъж на 5 години) и порьозната маса на ацетиленовите бутилки (веднъж годишно).
Строго забранено е съхраняването на смазочни материали и мазнини в близост резервоари за кислород, Петролните контейнери трябва да се измият 2-3 пъти с горещ 10% алкален разтвор преди заваряване и след това да се продуха с пара или въздух, за да се отстрани миризмата. Пълното прочистване трябва да се извърши преди заваряване на газопроводи.
Защита срещу отравяне от вредни газове, прах и дим. Замърсяването на въздуха от тези фактори се наблюдава особено силно при работа с електроди с висококачествено покритие. В същото време количеството прах и газове е много по-малко при автоматичното заваряване, отколкото при ръчното заваряване. Прахът за заваряване е в неговата физични свойства аерозол, състоящ се от суспендирани частици от минерали и метални оксиди в газообразна среда. Основните компоненти на праха са железни оксиди (до 70%), хром, манган, силиций, а също и флуоридни съединения. За тялото най-вредните съединения са флуор, манган и хром. От газовете, отделяни по време на заваряване в работни помещения, най-токсични са оксидите на въглерода, азота, водородния флуорид и други. Следователно, за да се премахне прахът и вредните газове от зоната на заваряване и да се осигури чист въздух, е необходимо да се организира обща и локална вентилация. Общата вентилация трябва да се извършва чрез снабдяване и изпускане, докато локалната вентилация трябва да бъде с горна, долна и странична всмукване, осигуряваща отстраняването на прах и газове директно от зоната на заваряване. Строго е забранено да се работи в затворени съдове без вентилация, което се състои в подаване на свеж въздух към работната зона на заварчика чрез маркуч. Количеството на доставения въздух трябва да бъде най-малко 30 m3 / h.
С ръководство електродъгово заваряване с електроди с висококачествени покрития, обемът на вентилация трябва да бъде 4000-6000 m3 на 1 kg консумация на електрод, при заваряване в въглероден диоксид - до 1000 m3 на 1 kg разтопен проводник, а за автоматична дъгова заваряване - около 200 m3. Разрешава се използването на естествена вентилация, ако часовата консумация на електродите е по-малка от 0,2 кг на 1 м3 помещение. Освен това при работа с оборудване за заваряване (рязане) на газ трябва да се спазват следните изисквания.
Преди заваряване трябва внимателно да прочетете инструкциите за употреба и технически характеристики различно оборудване (горелки, резервоари, скоростни кутии, маркучи). В този случай, ако не разполагате с достатъчно практически знания, за да извършите тези работи, тогава трябва да се консултирате със специалисти (можете да имате газ заварчик).
Новото оборудване трябва да се експлоатира само по време на гаранционния период, което гарантира безопасността на работата. Необходимо е внимателно да се тества, регулира и регулира оборудването във времето, посочено в информационния лист. Освен това изпитването и ремонта могат да се извършват само от специалисти. Забранено е да се произвежда заваръчни работи и инсталиране на оборудване в близост до запалими материали. По време на периода на експлоатация не е позволено да се напуска генераторът без надзор, а също и да се движи зареден генератор. Мобилните ацетиленови генератори трябва да се инсталират на разстояние най-малко 10 m от източниците на пожар. Тези генератори трябва да се инсталират вертикално и да се пълнят само с вода до препоръчаното ниво. Необходимо е генераторът да се зареди с калциев карбид само с гранулата, която е записана в паспорта на автомобила. След натоварване на определеното вещество генераторът трябва да се изчисти от въздушния остатък. За да се предотврати замръзване на генератора, е необходимо да се отстрани водата след работа. Ако генераторът е все още замразен, тогава той може да бъде затоплен само с пара или кърпа, напоена с гореща вода, но не и с открит пламък. Утайката трябва да се разтовари само след окончателното разлагане на карбида и само в утайките с надпис за забрана на тютюнопушенето.
Наличието, годността и зареждането на водния уплътнител на генератора е необходимо условие за безопасна работа на тази инсталация. Преди работа е наложително да се инсталира течност с ниско ниво на вода или ниско замразяване (30% разтвор на калциев хлорид във вода или 60% разтвор на етилен гликол във вода), която се зарежда при температура на въздуха под 0 ° C през смесителния кран. В уплътнението на водата нивото на течността трябва да бъде настроено на височината на контролния кран. След заваряване вентилът трябва да се промие с вода. Водното уплътнение трябва да се проверява за херметичност веднъж седмично и на всеки 3 месеца да се разглобява за почистване и измиване; След сглобяването трябва да разберете надеждността на уплътнението на възвратния клапан.
Калциевият карбид трябва да се съхранява само в херметически затворени барабани, които трябва да се съхраняват в добре проветрени и сухи помещения. Когато отваряте барабана, не можете да използвате стоманено длето и чук, за да предотвратите образуването на искри, които са много опасни за смеси от ацетилен-въздух. Отварянето е разрешено само със специален нож, а капакът е предварително покрит с масло в мястото на разреза (можете да пробиете дупка и след това да го отрежете с ножици). Медните инструменти не трябва да се използват, тъй като ацетиленът във влажни условия може да образува ацетиленова мед с мед, която е силно експлозивна, дори и с малки въздействия.
Фиксирането на скоростната кутия върху цилиндъра трябва да се извършва внимателно, за да не се наруши нишката; Монтажът трябва да бъде стегнат. Подаването на кислород към скоростната кутия се извършва само с напълно отслабена регулираща пружина на скоростната кутия и вентилът трябва да се отваря бавно. В същото време се уверете, че няма изтичане на кислород. Ако се установи някаква неизправност, тя трябва да се отстрани, след като вентилът на цилиндъра е предварително затворен.
Маркучите за подаване на газ трябва да бъдат плътно и плътно прикрепени към зъбците за затягане на нипелите. Мониторингът на здравето на газопроводите и маркучите трябва да се извършва непрекъснато. Строго е забранено да се намалява налягането на кислорода на входа на ножа под налягането на горивото в резервоара; свържете повече от една горелка към един затвор; да се използва фенер или горелка, която не е снабдена с възвратен клапан, който предпазва маркуча от проникване на пламък в него; движете се с работеща горелка, а също така оставяйте без надзор нож или горелка със запален пламък.
Не започвайте заваряване при липса на противопожарно оборудване (пожарогасител, варели или кофи с вода, кутии с пясък и лопата); пушене при работа с калциев карбид, течни горими вещества и ацетиленови генератори; да се използва кислород за раздуване на дрехи, както и да се използват инструменти на собственото ни производство.
Местата на газопламъчните работи трябва да бъдат добре почистени от експлозивни и запалими вещества на разстояние 30 m. от мобилни генератори. Ако пламъкът и искрите са насочени към източниците на енергия, тогава, за да ги защитите, трябва да се използва метален екран. Газовите съдове в съдове и резервоари трябва да се изпълняват с азбест или платно; лице, работещо в плавателен съд, трябва да има обезопасително въже, обезопасителен колан, лични предпазни средства с приток на чист въздух.
Този вид рязане на метал се отнася до термични методи и се използва широко в различни видове инсталационни и ремонтни операции. Характеристика на газовото рязане (както и други) е, че тя може да се използва за работа със заготовки със значителна дебелина, докато производителността остава на доста високо ниво.
Експертите отбелязват лекотата на използване на този вид рязане, тъй като технологията осигурява пълна автономност, независимост от източниците на електрическа енергия. Често капитанът се намира в ситуация, в която има храна в обекта, и е невъзможно да се свърже с него на работното място (да не говорим за полевите условия).
Преди да се разгледа технологичната технология, си струва да се даде обща концепция за газовото рязане. С негова помощ е възможно да се режат заготовки с такава дебелина, за които друг метод не е подходящ (но все пак, с увеличаване на този параметър на пробите, скоростта на рязане спада значително). Друг "плюс" - необходимия набор от оборудване е най-евтиният. Но си струва да се отбележат и недостатъците.
Когато обработвате метали на ръка, е доста трудно да се постигне висока точност на рязане, нейното качество. Това е възможно само за висококвалифицирани професионалисти с богат практически опит. Ако капитанът не е „обработил“, в повечето случаи ръбовете трябва да се обработват допълнително.
Извършването на по-фина работа, например на извито изображение или рязане на лист с големи размери по отношение на праволинейността, се извършва с помощта на специални преносими устройства (газови машини за рязане). Въпреки това, те все още се управляват ръчно.
В стационарни условия, в големите предприятия, за тази цел се използват цели CNC машини. С тяхна помощ можете, освен това, да запоявате ампули, да заварявате термодвойки, да извършвате локално закаляване и редица други операции, като извършвате наистина „бижута“.
Какви метали (сплави) могат да се режат ръчно? Почти всичко, с изключение на - месинг, алуминий, мед, "неръждаема стомана".
Разгледайте основните видове газово рязане на метали:
кислород
Температурата на метала се увеличава от газовия нагревател и рязането и отстраняването на образуваните оксидни частици се извършва с кислороден поток.
Поток на кислород
Разликата е, че потокът () се доставя допълнително към участъка на разреза. Химичният му състав влияе върху свойствата на метала, което го прави по-гъвкав. Това значително улеснява работата на рязане. Използва се по-рядко.
Защо да използваме 2 вида газове? Материалът (метал, сплав) се нагрява от ацетилен или пропан, а разрушаването на структурата (директно нарязана) осигурява чист кислород.
След като "нагревателят" доведе температурата на третираната зона до стойност от около 1000 - 1100 ºС, към него се подава струя кислород, която веднага се запалва. Процесът на рязане на материала се осигурява от неговата непрекъснатост и равномерно движение по определената линия (контур). Резачките се предлагат в различни модели.
Към тях могат да се приближат или 3 маркуча (2 за газов нагревател и 1 - за кислород), или 2 (един от които е кислород). По същия начин регулиращите клапани могат да бъдат 1 или 2. Но принципът на действие остава непроменен и лесно се разбира от тази фигура.
Разбира се, как да „доведете” горелката (прогресивно, без отклонения). Но защо стабилността на пламъка е толкова важна? Ако тя изгасне, металът ще започне да се охлажда рязко (особено при работа на открито). Ето защо, преди да започнете да режете, ще трябва отново да се нагрее отново.
Кислородно „копие“
По-съвършена техника. Същността на процеса е, че повишаването на температурата в областта на третираната зона се осигурява от така наречената "газова тръба" (копие). В същото време през него, под налягане, се подава кислород. Какво дава това? Рязането на метали с точка на топене под 600 ° С не си струва горните методи. В този случай целият процес ще се сведе до баналното премахване на повърхностния слой, а чрез прорязване няма да работи. И в някои случаи прекомерното нагряване на материала до високи температури може да доведе до разрушаване на неговата структура.
Ето защо сега се използва тази усъвършенствана технология, при която и отоплението, и рязането се извършват паралелно. Това се постига чрез използване на фенерче със специфичен връх. За разлика от по-старите аналози, има 3 дюзи. Принципът на неговото функциониране е ясен от фигурата.
Какво оборудване е необходимо
- Режещ газ с миксер. По правило за метода „кислород” не се използват моделите Р1-01П („стари”, за заваръчни работи не се прилагат!), РП2 (или 3) -01 (по-нови).
- Редуктор. Служи за намаляване на налягането на входящия газ до желаната стойност. На него се закрепват 2 манометра (измерване на входа и изход от адаптацията).
- Устройство за регулиране на налягането.
- Цилиндри с клапани. В един - кислород, в другия ацетилен или пропан. Понякога смес от тези два газа се използва като "нагревател", ако е необходимо да се отреже материал с повишена якост. Но такова оборудване е доста скъпо.
- Свързващи маркучи (високо налягане).
Как да се подобри качеството на среза? Има доста прост и евтин начин. За целта опитни заварчици използват “шаблони” (това е жаргонен термин за специални облицовки). Те осигуряват шев близо до идеала.
В статията са представени само общи концепции за газовото рязане. Преди да започнете работа, трябва да знаете нещо друго. Например, как правилно да регулирате натиска, на какво разстояние да държите ножа, особено работа с различни видове метали и много други нюанси. Но това вече е тема за друг разговор.
Фирма "MetiStr" извършва газово (кислородно) рязане на метални листове с дебелина до 300 мм. Работите се извършват от опитни оператори на автоматизирано немско оборудване на конкурентни цени и с отстъпки.
Газово рязане на метал в LLC MetiStr
дебелина mm | черна стомана, разтривайте. (Макс) | черна стомана, (разтрийте) мин | вмъкни, разтрийте / парче. |
---|---|---|---|
10 | 85 | 60 | 10 |
12 | 90 | 80 | 30 |
14 | 90 | 80 | 30 |
16 | 115 | 110 | 30 |
20 | 140 | 130 | 30 |
25 | 180 | 170 | 60 |
30 | 220 | 200 | 60 |
40 | 300 | 250 | 60 |
50 | 350 | 300 | 60 |
60 | 420 | 370 | 60 |
70 | 500 | 450 | 100 |
80 | 550 | 480 | 100 |
90 | 700 | 540 | 100 |
100 | 800 | 600 | 100 |
120 | 1100 | 700 | 300 |
150 | 1600 | 900 | 300 |
200 | 2000 г. (договор) | 1300 | 300 |
В процеса на газовото рязане, потокът от чист технически кислород въздейства върху метала, предварително загрят до + 1300 ° С. Тя изгаря детайла, като го реже на правилното място за оператора.
При газовото рязане се образува железен оксид, който в разтопеното състояние се издухва от работната зона. Този метод позволява обработването на всяка въглеродна и легирана стомана с дебелина от 1 до 300 mm.
Предимствата на газовото рязане на метал
Този метод на обработка на метални заготовки се използва както в черната, така и в цветната металургия, както и в машиностроенето, строителството и други индустрии. Предимства на газовото рязане:
- ниски разходи за обработка на метали;
- възможност за работа с листове със значителна (до 300 мм) дебелина;
- минималната ширина на производството от струята кислород;
- висококачествено рязане под всякакъв ъгъл на повърхността;
- не се изисква допълнителна обработка на ръбовете.
Компанията изпълнява тези поръчки повече от двадесет години, което води до голям практически опит. Днес фирмата е в състояние да преработва с газово рязане до 20 хил. Тона метал с дебелина от 4 до 300 мм. Специалистите на компанията успешно обработват всяка стомана, варираща от St3, 09G2S и завършвайки с високоякостни марки като HARDOX и WELDOX.
Постигнатите обеми на газовото рязане на метал станаха реалност благодарение на внедрения комплекс от технологични решения. Те включват:
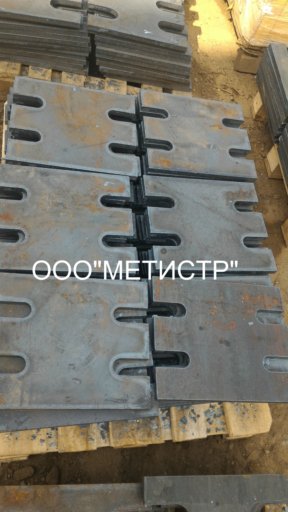

- автоматизация на този процес;
- използването на високо чисти технологични газове;
- използване на модерно оборудване (например, специално оборудване на немската фирма Messer Cutting & Welding GmbH);
- новаторска газоразпределителна система;
- стриктно спазване на технологичните инструкции на фирмата Messer.
В допълнение, инсталациите за газово рязане на метал, с работни участъци от 3x12 метра, са обединени в локална компютърна мрежа. Това ви позволява да оптимизирате процеса на рязане и да минимизирате материалните отпадъци.
Благодарение на изброените по-горе фактори, качеството на газовото рязане се подобрява, няма „увисване“ на метала и „купчините“ на ръба. Също така елиминира прекомерното прегряване на детайла. За нанасяне на покритие след газовото рязане е достатъчно лесно да се отстрани скалният слой на метала.
Активно е използвано рязане на метал чрез заваряване до определен период от време, като основен метод за обработка метални конструкции у дома. В резултат на рязане не се различават по красота, така че използването на мелница значително натискане на заваряване. Методът, който е тестван през годините, все още се използва, а възможностите му са разширени чрез използването на ново оборудване.
Заваряване на метали в следните случаи:
- на полето, когато няма източници на електричество,
- има нужда от рязане на много дебел метал,
- когато режете, трябва да получите сложна форма,
- необходимо е металът да се реже на трудно достъпно място.
Заваряването се отнася до универсални процеси, които могат да бъдат съединени и разделени на части. Следните опции за оборудване за рязане на метал са най-приложими у дома:
- дъга (инвертор),
- газов резач
- плазмен резач.
В тази статия ще говорим подробно за характеристиките, технологията и основните принципи за рязане на метал. заваръчен инверторметалообработване на газ чрез използване на кислород и пропан, и o плазмено рязане метал. След като изучава основните принципи на работа с различни видове оборудване, можете да извършвате рязане на метал със собствените си ръце.
Дъгово рязане
Когато изучавате основите на заваряването, новакът най-много се страхува да изгори метал и напълно да унищожи ставата. При рязане на метал целта на заварчика е точно да гори, за да отреже метала.
За да се отреже металът от дъгата, е необходимо да се загрее до температурата на топене и да се отстрани разтопения метал от зоната на заваряване. Отстраняването се извършва под собственото тегло на разтопения метал, поради натиск от дъгата или въздушния поток, подаван към зоната на заваряване.
За рязане на метал се използват следните електроди:
- покрит метал,
- въглища,
- тръбна,
- волфрам.
Този метод се използва за рязане на стомана, включително легирани, цветни метали и сплави.
Недостатъците включват ниско качество на рязане, груби ръбове, наличие на скала. Следователно, ако металът продължи да създава структури, ръбовете трябва да бъдат допълнително обработени, например почистени.
Рязането се извършва на същото оборудване като заваряването във всички пространствени положения. Преди това като домакински уред се използваше трансформатор или изправител, а сега инверторът се използва най-често.
Основи на рязане на дъга
За да се отреже металната дъга настройте силата на тока с 30-40% по-висока, отколкото при заваряване. Запали силна дъга на горния ръб на метала и слез, докато режеш ръба.
Инвертор за рязане на метал
За рязане изберете електроди с малък диаметър, но токът, напротив, излагайте повече, отколкото е необходимо за заваряване. Например, по диаметъра на електрода 2.5 mm, задайте 140А.
Запали дъгата и остави електрода на едно място. Опитвайки се да се удължи дъга, сякаш изгаряше метал.
Ако плочата е поставена вертикално, разтопеният метал леко ще се източи. В случай на хоризонтално рязане на метал със заваръчен инвертор, зацапванията ще се събират на дъното на плочата.
За да се гарантира най-доброто загряване на метала, при рязане те поемат директна полярност. В този случай, металът се затопля дълбоко, но се оказва, че отрязъкът е тесен.
Видеото показва какви възможности се отварят при прилагане на рязане на дъга. Табела с дебелина 10-20 мм се изрязва буквално за няколко минути с лекота и красота.
Рязане с газов фреза
Доскоро металотърсачът оставаше основният метод за разделяне на металите, особено ако се налагаше да се реже чрез сложен контур, да се обработи ръб или да се получи дупка. Предимството е, че за извършване на работата няма нужда от източник на електричество.
Рязането на метал с газов режещ апарат се извършва по следния начин: смес от кислород и запалим газ се запалва, като получената горелка нагрява метала в зоната на рязане до температура на горене най-малко 12000 ° С. Дайте поток от кислород.
Металът се запалва и се получава линията на рязане. За рязане най-често се използва кислород, смесен с пропан. Както въглеродните, така и легираните титанови сплави се обработват с газово рязане.
Газово рязане на метал върху смес от пропан и кислород
Преди започване на работа, металът се подготвя: те почистват мръсотия, мазнина, скала, ръжда.
Оборудване за газово рязане
За извършване на газови рязане се изискват по-малко умения, отколкото при заваряване, защото няма нужда да се гарантира херметичността на връзката. Оборудването ще изисква газорезачка, кислородни бутилки и пропан.
Всеки цилиндър има регулатор на налягането. Газът от цилиндъра към скоростната кутия се подава чрез маркуч за високо налягане.
Преди да започнете работа, издухайте маркучите, за да отстраните замърсяванията. Всички маркучи се проверяват, връзките с редуктора, всички разглобяеми връзки се проверяват за течове.
Те проверяват работоспособността на самия нож и го продупчават с кислород. За да направите това, свържете цилиндъра с кислорода до мястото на закрепване на кислородния маркуч. Газовият цилиндър още не е свързан. Монтирайте на скоростната кутия 5 атм и отворете двата клапана на ножа. Като вдигнете пръста си към второто зърно, можете да наблюдавате дали има теч. Ако това не е възможно, каналите на режещите машини трябва да бъдат прочистени.
Работен ред
Газовото рязане се извършва чрез запазване на пропорцията: 10 части кислород към 1 част от газа. Следователно, те се монтират на газовия редуктор 0.5 в, и на кислородния редуктор 5 в.
Първо, пропанът се отваря леко и газът се запалва. Дюзата лежи върху метала и постепенно започва да доставя кислород. Чрез завъртане на клапаните можете да регулирате размера на пламъка и да получите необходимия пламък за работа. Колкото по-дебел е металът, толкова по-силен трябва да бъде пламъкът, което изисква голямо количество газ и кислород.
Внимание: Пламъкът се регулира чрез регулиране, а не рязане на кислородно налягане.
Горещият пламък се довежда до метала на мястото, където трябва да се направи разрезът, като се поддържа разстоянието между дюзата и метала от 5 mm. Под действието на пламъка металът се загрява до необходимата температура. Това се случва бързо, след няколко секунди. Наблюдавайки процеса, те забелязват, че в този момент металът се намокри. Запалва се само металът и кислородът за рязане веднага се включва.
За да се избегне удар на пламъка, който може да бъде съпроводен с пляскане, постепенно се включва рязането на кислород.
В този случай кислородът ще светне веднага щом докосне горещата повърхност на метала. Видеото показва как с помощта на газовото рязане можете да изрязвате форми на най-сложната форма.
Качеството на рязане се влияе от скоростта на заваряване. Контролирайте скоростта, като се съсредоточите върху искрите в зоната за рязане. Ако искрите са напред, това означава, че скоростта е недостатъчна. При висока скорост искри са зад режещия инструмент, в този случай е трудно да се отреже качествено детайла.
За да се направи дупката, мястото се нагрява до желаната температура, като се подава кислород. Металът е запалим. Режещият инструмент се подава в металната зона и се пробива отвор.
Рязане на метал с плазмен нож или плазмен режещ инструмент
За възможностите на плазмената горелка е добре описано във видеото. След гледане на видеоклипа със сигурност ще искате да имате такова прекрасно оборудване във фермата, въпреки високата му цена.
Рязането на метал става под действието на плазмената енергия. Оказва се, както следва. Когато бутонът за запалване е натиснат, токът се подава от източника и се създава дежурен служител в плазмената горелка. заваряване дъга, Сгъстеният въздух преминава през него, йонизира се и плазмата се издърпва през дюза с висока скорост. Плазмата има температура над 10 хиляди градуса и скоростта е два пъти по-голяма от скоростта на звука. Тази енергия е достатъчна, за да се разтопи металът и дори да се изпари.
Операторът довежда плазмения режещ инструмент до мястото, където трябва да се направи среза, и металът започва да се топи. Скоростта на ръчното движение трябва да осигури метално рязане. Параметрите на рязане са сила на тока и налягане на въздуха.
Подробности за това как се произвежда плазмата и как се подрежда ножът, са добре показани във видеото.
При неправилно избрани параметри върху ръба може да се образуват шлаки. След края на рязането не изключвайте веднага подаването на сгъстен въздух. Изпълни известно време, за да охлади метала.
Технология, работеща с плазмен нож
Преди започване на работа почистете ръбовете, отстранете замърсяванията и ръждата от тях.
Плазменото рязане на какъвто и да е метал започва с монтирането на сила на тока. Принципът е прост: силата на тока се изчислява в зависимост от дебелината на метала. Величината на тока, която е необходима за рязане на 1 мм дебелина на метала, умножена по дебелината на метала, която трябва да се отреже. Ако е необходимо да се изреже 25 мм стомана, тогава е необходимо да се умножи 25 с 4А (ток, необходим за рязане на 1 мм стомана или чугун). Общо излагане на оборудването 100А.
Скоростта, с която трябва да режете, влияе директно върху качеството на работа, но зависи от умението на ножа. Експертите съветват в началния етап на работа да се съсредоточи върху наличието на искри от гърба на продукта. Ако те липсват, металът не се изрязва напълно.
Преди започване на дъгата за половин минута режещият инструмент се продухва с газ, за да се отстрани замърсяването и възможния конденз. След това операторът натиска бутона за запалване на пилотната дъга, свети за 2 секунди. Ако дъгата на рязане не се образува, процесът се повтаря отново.
В зависимост от модела, запалването може да бъде контактно и безконтактно:
- При контакт с късо съединение е необходимо. Веднага след като плазмата напусне дюзата, между метала и електрода се образува плазмена дъга и започва процесът на рязане.
- В случай на безконтактна дъга се запалва между дюзата и електрода. Когато дюзата се доближи до метала, се образува работна дъга.
По време на рязане е необходимо да се поддържа постоянна дължина на дъгата. Ако не е снабден със специален стоп, тогава режещият инструмент може да издържи този параметър, трябва да бъде между 1,6 и 3 mm.
По време на работа е необходимо дюзата да се държи до метала под ъгъл от 900 °. За да се намали напрежението тънък металгорелката се държи под лек ъгъл. По време на рязане обърнете внимание на метала, който не запушва дюзата на горелката.
Подробности за работата на плазмената горелка, вижте видеото.
С помощта на разгледаните методи за рязане можете да изрежете метала по най-сложния контур. Тези работи могат да се извършват ръчно, след малко теоретично и практическо обучение. Основното е наличието на оборудване и свързани с него материали.
Ръчното газово рязане е най-разпространеният, прост и високоефективен начин за рязане на ламарина. Ако по-ранното рязане на ламарина се извършваше чрез механични методи, например мелница, то сега те се използват само в случаите, когато не е налично заваръчно оборудване. Рязането на лист с газ се различава от механичното с по-голяма точност и скорост, способността да се режат дупки, а с помощта на допълнителни дюзи е възможно да се реже под скосяване, пръстен или фигура. наръчник газово рязане Листовият метал е по-популярен от машината поради ниската си цена.
Услугите за ръчно рязане на ламарина се извършват с помощта на газови горелки. Устройствата за рязане на газове с кислород са малки по размер, лесни за транспортиране и независими от източници на енергия, което им позволява да се използват навсякъде.
Ръчното рязане на ламарина е високо търсено в различни области на дейност. Той служи за разглобяване на метални конструкции, нарязване на заготовки или производство на единични части от ламарина, изрязани ръбове, отпадъци от тапицерии, прегради и в други случаи, когато не е възможно да се използва машинно рязане или е икономически неоправдано, например по време на ремонтните работи.
Първата газова горелка, работеща върху сместа ацетилен-кислород, се появява през 1901 г. във Франция. Той е проектиран от инженери Чарлз Пикар и Едмон Фуше. Оттогава дизайнът му почти не се е променил.
Обикновено ръчно рязане на ламарина, което не изисква висока прецизност на рязане, се извършва с помощта на просто устройство, състоящо се от газови бутилки, регулатори на налягането, маркучи, смесители и. \\ t газова горелка.
Рязането с газова горелка може да се използва за рязане на ламарина с дебелина до 300мм. Autogen е добре изрязана стомана, чиято точка на топене е по-висока от температурата на тяхното изгаряне в поток от кислород, в противен случай металът ще се стопи, преди да започне да гори в кислород. Нисковъглеродните и нисколегираните сплави с фракция на въглеродно съдържание до 0,3%, които се топят при 1500 ° C и се запалват при 1300 ° C, напълно отговарят на това условие.
Газовото рязане на ацетилен от листов метал и кислород се извършва на няколко етапа. Преди започване на работа повърхността на отрязания метал трябва да се почисти по линията за рязане от мащаб, ръжда, боя и други замърсители. След това мястото на разреза се нагрява с ацетилен до температурата на запалване на метал в кислорода от 1000 до 1250 ° C, в зависимост от вида на стоманата. След това към нагрявания метал се изпраща мощна, тясно насочена струя кислород под високо налягане до 12 атмосфери. Когато струята достигне нагретата повърхност, тя се запалва от контакт. Газовото рязане на ламарина се извършва в резултат на продължително продължително излагане на гореща струя кислород върху метала, който се окислява, стопява, изгаря и изгаря до пълната си дебелина. Резултатът е сравнително широк разрез с неравномерни втвърдени ръбове, което изисква допълнителна обработка, тъй като образуването на скала, потоци и оксиди е възможно, когато металът се комбинира с изгаряне на кислород.
Ръчното рязане на ламарина с автоген има най-ниска цена в сравнение с други термични методи. Цените на услугите за ръчно кислородно рязане на метални листове зависят от дебелината и химичния състав на метала, който ще се реже, използваното оборудване, времето, вида и качеството на рязане. Разходите за рязане на ламарина се изчисляват индивидуално. Цени кислородно рязане Може да се научи металопрокат, като се свържете с нашите експерти по всякакъв удобен за вас начин.
Също така в нашия сервизен метален център има следните видове рязане на ламарина.