Electrodes de surfaçage résistantes à l'usure par abrasion
L’un des moyens les plus simples et les plus efficaces permet non seulement de rétablir l’adéquation (performances) des pièces. En soudant un métal avec une électrode, vous pouvez modifier la forme de l'échantillon, lui conférer d'autres propriétés (différentes de l'original), augmenter sa résistance et sa résistance à l'usure. Quelle est cette technologie, quelles sont ses fonctionnalités et est-il possible de mettre en œuvre dans la vie quotidienne - le sujet à considérer dans cet article.
- Il est peu probable que le lecteur s'intéresse aux technologies industrielles et, même avec l'utilisation de la robotique, l'accent est mis davantage sur la technique de soudage des métaux avec des électrodes au niveau des ménages, c'est-à-dire avec leurs propres mains.
- Souvent, les alliages, par exemple l'acier, sont également appelés métaux. Les technologies et les composants individuels (par exemple, la marque d'électrode) peuvent différer légèrement d'un cas spécifique à l'autre. Dans un article, il est impossible de couvrir littéralement toutes les nuances. Par conséquent, avant de procéder au surfaçage, vous devez clarifier certains points concernant les métaux utilisés. Tout ce qui est noté ci-dessous ne constitue que des recommandations générales, ainsi que la requête elle-même, entrée dans la chaîne du moteur de recherche.
- Le revêtement étant un peu similaire au soudage bien connu, il sera utile de lire les articles sur la technologie de ce dernier en relation avec divers métaux et alliages - cuivre, aluminium, fonte, acier inoxydable et plusieurs autres, en fonction des spécificités du travail à effectuer.
Terminologie
- Surfacing - la connexion de métaux différents en les appliquant l'un à la surface de l'autre.
- Métal d'apport - qui est appliqué; la principale subit un traitement de surface selon cette méthode.
La technologie
La pénétration mutuelle des matériaux se produit au niveau moléculaire. Pour cela, la couche superficielle du substrat est chauffée pour fondre à une faible profondeur et l'additif est chauffé à l'état liquide. Une telle connexion est appelée homogène (du mot mixage, traduit de l'anglais) et se caractérise par une fiabilité accrue, car il est impossible de la diviser en «parties» d'origine par des moyens mécaniques.
Les avantages de cette technologie sont les possibilités de régler l’épaisseur de la couche (dans des limites considérables) et d’appliquer l’additif à des pièces (échantillons) de toutes formes.
Règles de base du flotteur
- La profondeur de la masse fondue de la couche supérieure de la base devrait être aussi petite que possible. L'un des moyens de remplir cette condition consiste à incliner l'électrode. Il est fait dans la direction opposée à la direction de son mouvement. Un mélange minimal de métaux dissemblables aide à réduire les contraintes résiduelles et à éliminer les déformations possibles dans certaines zones.
- L'excès d'additif complique le traitement ultérieur des pièces et nécessite plus de travail et de temps.
Technologie d'électrode
La préparation préalable du métal de base est obligatoire - décapage + dégraissage.
Le surfaçage par électrodes est la méthode la plus courante pour produire une couche homogène. En raison de la simplicité de la technologie, elle est considérée comme essentielle pour une utilisation en production et à la maison. En fonction du métal de base et des objectifs poursuivis, une électrode est sélectionnée avec le revêtement de surface approprié. En fonction de sa marque, la couche résultante acquiert les caractéristiques requises. La figure explique tout bien.
Schéma de connexion - direct ou inverse. Cette dernière option est utilisée plus souvent, car plus pratique. La tension est constante, donc «+» est sur l'électrode revêtue.
Caractéristiques technologiques
- L'épaisseur et la forme de la couche dépendent de la section transversale de l'électrode.
- Pour assurer une soudure de haute qualité, l'intensité de la tension et du courant de l'arc doit être minimale, ce qui nécessite une adaptation précise. Avec l'acquisition d'expérience pratique, la réalisation de cette condition n'est pas particulièrement difficile.
Ce que vous devez savoir
- L'augmentation de la tension conduit au fait que le "rouleau" ne croît pas en hauteur, mais en largeur. La longueur de l'arc augmente.
- Pour chacun - sa propre fonctionnalité d'application. Par exemple, est-il nécessaire de préchauffer la base? Pour aciers faiblement alliés ce n'est souvent pas nécessaire. Quel est le mode de refroidissement? Quel ensemble de courant? Toutes les nuances technologiques de la gaine sont reflétées dans la documentation pour des électrodes spécifiques.
- La qualité du surfaçage est meilleure, plus la température de chauffage est élevée. Pratiquement pour tous les alliages et métaux, sa valeur minimale est de + 300 ºС. À la maison, vous aurez besoin d'au moins un petit four (par exemple, un four à chambre électrique).
Points de câblage
Pour surfaces planes
Rouleaux étroits. Ils correspondent à environ un tiers de chevauchement.
Large. L'électrode se déplace perpendiculairement à l'axe du flotteur. Les mouvements oscillatoires, leur configuration (fréquence, amplitude) sont sélectionnés en fonction des dimensions de la base.
Technique combinée. Le surfaçage est fait avec des rouleaux étroits, mais ils sont situés à une distance légèrement inférieure à leur largeur. Après avoir retiré la base des scories dans de tels vides, le prochain flotteur est créé. Résultat: obtenir une couche homogène continue.
Pour obtenir une meilleure couverture de la base avec un autre métal, vous devez commencer à poser le prochain rouleau sur le côté opposé de la pièce. De plus, la superposition n'est pas cohérente, l'une après l'autre, mais de manière aléatoire, puis dans un domaine, puis dans un autre. Cela empêchera le substrat de se déformer partiellement en cas de surchauffe.
Pour cylindres
Les trois méthodes sont illustrées dans la figure.
Il existe une autre technologie de surfaçage des métaux utilisant des électrodes - dans un environnement gazeux protecteur. À la base, c'est simple. La difficulté est différente - vous devrez acheter une bouteille et la remplir avec le gaz approprié (argon, hélium ou autre), en fonction du type de métal d'apport. Cette option est plus appropriée pour un petit atelier. À acquérir bouteille de gaz pour le travail ponctuel à la maison est à peine conseillé. Par conséquent, cette technologie n'est pas prise en compte dans l'article.
Les recommandations sur le choix des électrodes et les spécificités de leur utilisation sont considérées par l'auteur comme superflues. Tout d’abord, toutes les informations nécessaires sont contenues sur l’emballage. Deuxièmement, le vendeur répondra à toutes les questions obscures. À certains moments, les gestionnaires sont bien familiarisés avec ces sujets et peuvent donner des conseils pratiques.
En règle générale, les soudeurs doivent constamment traiter avec différentes qualités d'acier. En même temps, il n’existe pas de marque universelle d’électrodes capables de souder avec la même efficacité de différentes qualités d’acier et les spécialistes devraient en tenir compte. caractéristiques techniques pendant le travail avec tel ou tel métal.
Classification des électrodes
Les électrodes destinées à sont divisées en plusieurs groupes ayant des paramètres spécifiques corrélés avec des composants d'alliage de différentes qualités d'acier. Nous énumérons les types d'électrodes les plus courants pour le surfaçage en acier et présentons leurs caractéristiques.
- Électrodes de soudure faible acier au carbone avec une faible teneur en éléments d'alliage. Ces nuances d'acier sont très résistantes à l'usure par abrasion et aux chocs.
- Électrodes conçues pour le soudage des aciers faiblement alliés à teneur moyenne en carbone. De telles nuances d’acier sont très résistantes au frottement et souder capable de résister à des températures allant jusqu'à 650 degrés.
- Électrodes pour le soudage des aciers au carbone alliés et fortement alliés. La couche de métal déposée lors du soudage résiste à l'abrasion et aux chocs.
- aciers alliés à haute teneur en carbone résistant à la haute pression. Les électrodes de ce groupe sont utilisées pour travailler sous haute pression. Le joint de soudure est capable de résister à des températures allant jusqu'à 850 degrés
- Ce groupe comprend des électrodes pour le soudage de nuances d'acier austénitique (inoxydable) fortement allié. Les caractéristiques des consommables permettent d'obtenir un joint en acier inoxydable lors du soudage.
- Électrodes pour le travail avec des nuances d'acier résistant à la chaleur, capables de résister à des températures supérieures à 1000 degrés.
Tous les types d'électrodes ci-dessus sont conçus pour un usage industriel et domestique.
La composition et la structure des électrodes
Pour obtenir les qualités requises pour un soudage efficace de divers types d’aciers, les tiges d’électrodes de différents types sont sélectionnées en fonction des marques de métaux à souder.
La composition et la structure des électrodes déterminent en grande partie l'efficacité du surfaçage à l'arc et les propriétés de la couche métallique déposée.
Outre les éléments qui constituent la base du métal à souder, la composition des produits consommables est complétée par des additifs qui améliorent et facilitent le processus de soudage. Ainsi, les électrodes de la marque UONI 1345 contiennent les éléments suivants:
- manganèse
- carbone
- silicium
- phosphore
Mais les électrodes de la marque OZN 6, destinées au soudage des aciers résistant à la chaleur, contiennent dans leur composition une proportion importante de titane, ce qui garantit la bonne qualité du surfaçage.
Grades d'électrodes destinées au surfaçage des aciers
Imaginez la marque d'électrodes la plus répandue pour le soudage de différents aciers.
- OZN 300M - utilisé pour le soudage de composants et de pièces en acier faiblement allié, soumis à une usure rapide.
- UON et 13NZh 20H13 - conçus pour le surfaçage d'aciers résistants à la chaleur pouvant supporter des températures allant jusqu'à 400 degrés.
- OZN 7 - électrodes pour le soudage de structures et d'éléments à haute charge.
- T 590 - pour les structures et pièces de soudage en aciers à haute teneur en carbone, non soumises à des charges élevées.
- OZI 5 - surfaçage de la couche usée des outils de coupe du métal et des moules d'estampage à chaud
- OZSH 6 - réparation d'équipements de forge, de machines et de composants fonctionnant dans des conditions de charges élevées et de températures extrêmes.
Sélection d'électrodes pour le surfaçage de différentes qualités d'acier
Lors du choix des consommables pour le soudage, il est nécessaire de prendre en compte la marque et la structure de l'acier à souder, ainsi que les dimensions des ébauches. Ainsi, pour le soudage de grandes pièces épaisses, il est nécessaire de choisir des électrodes de plus grande section, ce qui permettra à l’acier de fondre à une profondeur suffisante pour une connexion fiable. De plus, les électrodes de plus grand diamètre peuvent supporter des charges de courant élevées.
Actuellement, outre les principales marques, il existe de nombreux analogues à la production de sociétés nationales et étrangères. Pour sélectionner l'option optimale, il est nécessaire d'étudier en détail les propriétés des consommables et, autant que possible, de les corréler avec les propriétés des métaux à souder.
Brève caractéristique générale et catalogue des électrodes de surfaçage.
Le groupe d'électrodes pour le surfaçage comprend les marques destinées au soudage à l'arc manuel de couches superficielles aux propriétés spéciales (à l'exception des marques pour le surfaçage de couches de métaux non ferreux). Ils sont fabriqués et livrés conformément aux exigences des normes GOST 9466-75 et GOST 10051-75. Dans certains cas, le surfaçage est également utilisé. électrodes de soudurePar exemple, les nuances destinées au soudage des aciers fortement alliés résistant à la corrosion, à la chaleur et à la chaleur.
Selon GOST 10051-75, les électrodes servant au surfaçage des couches de surface sont classées en 44 types en fonction de la composition chimique du métal fondu et de la dureté à la température normale (par exemple, nuances de type E-16G2HM, E-110X14V13F2, E-13X16N8M5S5G46). Le métal de soudure de nombreuses qualités est réglementé par les spécifications des fabricants.
En fonction du système de dopage adopté et des conditions de fonctionnement du métal fondu résultant, les électrodes de surfaçage (électrodes de surfaçage) peuvent être divisées de manière arbitraire en 6 groupes:
Le groupe d’électrodes de surfaçage est représenté par des repères destinés au surfaçage manuel des couches superficielles de pièces usées. Une telle couche de soudure présente des propriétés spéciales (à l’exception des types d’électrodes destinées au soudage de pièces en métaux non ferreux). Les électrodes de surtension sont fabriquées et livrées conformément aux exigences des normes GOST 9466-75 et 10051-75.
Dans certains cas, des électrodes de soudage, telles que des marques conçues pour le soudage, et des aciers résistant à la chaleur sont également utilisés pour les travaux de surfaçage.
Les électrodes de surfaçage pour la restauration des couches de surface selon GOST 10051-75 en fonction de la dureté et de la composition chimique du métal déposé à température normale sont divisées en 44 types (par exemple,-13Х16Н8М5С5Г46,-110Х14В13Ф2,-16Г2ХМ). Les fabricants de nombreuses marques réglementent le métal soudé avec des conditions techniques.
Division conditionnelle en groupes
En fonction des conditions de travail et du système de dopage adopté pour le métal obtenu, les électrodes de soudage (électrodes de soudage) sont classiquement divisées en 6 groupes. (Par exemple, ci-dessous les tampons / types d'électrodes (types de métal), les liens vers toutes ces marques sont plus loin sur cette page):
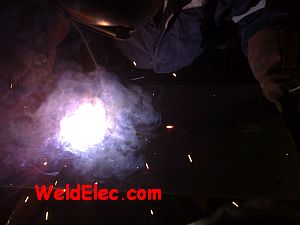
Electrodes de surfaçage résistantes à l'usure par abrasion
Le surfaçage est une méthode d'application d'une couche de métal en fusion, un métal d'apport, sur le noyau. Les électrodes à souder, résistantes à l'abrasion, créent une nouvelle couche sur les pièces présentant d'excellentes propriétés mécaniques. En raison de leur utilisation, vous pouvez:
- apporter le produit à son apparence d'origine,
- le ramener aux dimensions géométriques
- donner de nouvelles qualités précieuses
- augmenter la résistance à l'usure, la capacité de résister aux effets de la température.
Les travaux de terrassement, les maillons des chaînes de chenilles, les godets des excavatrices, les couteaux de bulldozer, les pointes des défonceuses sont soumis à l’abrasion. Protégez ces pièces des charges et de la destruction en appliquant la marque d'électrode et ,. Leur tige est en acier au carbone, le plâtre contient du ferrobore, du carbure de bore, du ferrochrome et du ferrotitane.
Electrodes résistantes aux chocs pour le surfaçage
Les électrodes de surfaçage résistantes aux chocs sont utilisées dans la réparation des équipements de concassage tels que les tiques, les morsures, les armures et les rouleaux, les cônes et les bâtiments. Ces marques sont utilisées comme elles s'appelaient OK 86.08, T-590 et T-620. Avec eux, vous pouvez souder quatre couches ou plus. Le T-590N est conçu pour ceux qui ont décidé de réparer la pièce et de l’oublier longtemps.
Marque la couche de soudure T-590 et T-620 non soumise à la formation de fissures lors de l’impact. Ils sont résistant à l'usureIls sont bien connectés au métal de base, ils aident à prolonger plusieurs fois la durée de vie des produits.
Électrodes de rechargement carbure
Les électrodes en carbure utilisées pour le surfaçage aident à restaurer la géométrie de nombreux types de pièces. Marques bien adaptées, et ESAB OK 84.42 (discontinué) pour l'acier non allié. Il est possible de souder des produits en acier au carbure soumis à l'abrasion et à l'impact avec l'UTP PUR 600, ESAB OK 83.53 (discontinué). Ils conviennent également à la restauration de l’instrument de mesure de coupe, des mécanismes fonctionnant à forte usure.
La couche de métal soudée à l'aide d'une électrode de marque tubulaire ne peut pas être usinée. Avec les alliages durs vous permet de travailler avec succès. Avec leur aide, réparez la surface des pistes, des couteaux, des seaux. Ils ont une dureté élevée de 55-63 HRC. Ils ont un diamètre de 3,2-12 millimètres.
Caractéristiques de soudage de certaines marques
ZELLER L61. Voir également le clip, où le dépôt par électrode ZELLER L61 est démontré.
Faits saillants sur les électrodes de surfaçage
IMPORTANT! Couche de métal soudé propriétés chimiques, la composition de l'électrode doit presque entièrement coïncider avec les caractéristiques de l'acier de la pièce réparée. Ceci est important à considérer lors du choix d'une marque, type.
Le principe de fonctionnement de la méthode de dépôt repose sur la fusion de l'électrode sous l'influence de arc de soudure, lors de la création d’une ou de plusieurs couches. Combien d’entre eux seront nécessaires pour déterminer, en accordant une attention particulière aux propriétés de la pièce, en fonction des besoins.
Les caractéristiques de qualité créées par la couche de soudeur sont obtenues en fonction de la profondeur de pénétration du métal. Cet indicateur devrait être minimal. Il est important de prendre en compte que vous devez obtenir le moins possible de mélange de l’acier déposé avec l’acier principal. Le soudeur doit essayer d’obtenir la contrainte résiduelle minimale et d’éviter la déformation de la pièce. Cette exigence ne peut être remplie qu'en observant les deux précédentes, choisir le bon électrode et ébullition minimale.
Il est important de ne pas dépasser les valeurs de tolérance autorisées lors du traitement ultérieur des pièces après le soudage.
Pour éliminer le gauchissement, le surfaçage est préférable dans des sections séparées, et il est conseillé de commencer à poser chaque rouleau suivant du côté opposé par rapport au précédent.
Ce n'est qu'en respectant ces règles simples que le dépôt de métal contre les effets nocifs des gaz est protégé. Il s'avère dense, ne pas avoir de pores, aucune sorte de couche de fissures et d'inclusions étrangères. Il est important de prendre en compte le fait que la surface de la pièce réparée doit être soigneusement nettoyée de l'huile, de la corrosion, de la rouille et de tout autre type de saleté avant de commencer les travaux de surfaçage.
Vidéo
Regardez la vidéo, où l’artisan construit la charrue:
Ceux qui exploitent divers mécanismes doivent parfois faire face au besoin de souder du métal à un endroit particulier du détail. Trou de montage cassé, surface usée pendant le fonctionnement, bord émietté des outils de coupe, coussinet usé. Dans tous ces cas, vous pouvez vous passer de la pièce à remplacer, en la restaurant par la méthode de surfaçage en métal de la pièce usée. Le surfaçage sur une pièce métallique permet non seulement de restaurer les propriétés originales du produit, mais également de lui donner de nouvelles qualités. En particulier, en soudant une couche de métal de carbure sur la base d'acier à faible teneur en carbone, un outil résistant à l'usure ou un outil de coupe peut être obtenu.
Le surfaçage consiste à appliquer un métal en fusion (appelé additif) à la surface d'un autre (appelé principal). Dans le même temps, le métal de base est également fondu sur une faible profondeur pour former un composé homogène. Le surfaçage peut avoir différents objectifs: restaurer la géométrie perdue de la pièce ou lui donner une nouvelle forme, former une couche de surface présentant les propriétés physiques et mécaniques souhaitées (dureté accrue, résistance à l'usure, résistance à la corrosion, à la corrosion, etc.), durcissement par soudage.
Le surfaçage peut être effectué sur n'importe quelle surface - plate, conique, cylindrique, sphérique. Dans de larges limites, son épaisseur peut varier de quelques millimètres à plusieurs centimètres.
Principes de base du surfaçage
Dans ses points principaux, la technologie de dépôt est similaire à la technologie de soudage. Il fait face aux mêmes tâches qu'avant le soudage - protéger le métal en train de se déposer des gaz contenus dans l'air, obtenant ainsi une densité, sans pores, sans fissures ni inclusions étrangères du métal fondu. Par conséquent, il est important de vous familiariser avec l’article général sur la soudure, les articles sur la soudure des métaux correspondants (soudure du cuivre, de la fonte, de l’aluminium, de l’acier inoxydable) et les revêtements d’électrodes, sans quoi, par exemple, pourquoi calciner les électrodes avant le surfaçage et quelles en seront les conséquences ne le faites pas, ou pourquoi la polarité de la connexion de l'électrode est importante. Lors du surfaçage, il est nécessaire de suivre les principes de base consistant en un certain nombre d'exigences:- Il est nécessaire de s'efforcer d'obtenir une pénétration minimale du métal de base. Ceci est réalisé en inclinant l'électrode dans la direction opposée au dépôt.
- Il devrait y avoir le moins possible de mélange du métal de soudure avec le métal principal.
- Nous devons essayer de minimiser les contraintes résiduelles et les déformations dans les pièces. Cette exigence est largement assurée par le respect des deux précédentes.
- Il est nécessaire de réduire à des valeurs acceptables les tolérances pour le traitement ultérieur de la pièce. En d'autres termes, vous devez souder le métal exactement autant que nécessaire et pas plus.
Différents procédés de surfaçage des métaux sont appliqués - arc électrique, gaz, électroslag, induction, plasma, arc pulsé, arc de vibration, surfaçage en poudre. Le surfaçage d'arc le plus répandu.
Les matériaux de surfaçage existent sous différentes formes. Il peut s’agir de tiges de remplissage, de mélanges de poudres, d’électrodes revêtues en surface et de fils fourrés et pleins. Pour le surfaçage à l’arc électrique, on utilise principalement des électrodes revêtues, des barres de remplissage et des fils.
Revêtement avec des électrodes enrobées
Le surfaçage avec des électrodes revêtues fait référence aux principales méthodes utilisées dans l’industrie et dans la vie quotidienne, en raison de sa simplicité, de sa commodité et du fait que des équipements spéciaux ne sont pas nécessaires. Un grand nombre de types d'électrodes sont produits, ce qui crée une couche de surfaçage présentant diverses caractéristiques qui fournissent les qualités requises de produits pour un fonctionnement dans certaines conditions.Faire surface nécessite certaines compétences dans le travail. Afin de ne pas augmenter la part du métal de base dans le métal soudé, il est nécessaire de faire fondre les deux composants avec un courant et une tension minimum. La composition du métal déterminera le type d'électrode, ainsi que l'épaisseur et la forme - le diamètre de l'électrode. La tension de l'arc détermine la forme du cordon de soudure: à mesure qu'elle augmente, la largeur augmente et la hauteur du rouleau diminue, la longueur de l'arc et l'oxydabilité des dopants, en particulier du carbone, augmentent. À cet égard, tendez à la tension minimale, qui doit être compatible avec le courant d'arc.
Le surfaçage des pièces en acier est effectué, en règle générale, par courant continu. inversion de polarité (sur l'électrode "plus") en position basse.
Les pièces en acier faiblement carboné et faiblement allié sont généralement déposées sans préchauffage. Mais souvent, un préchauffage et un traitement thermique ultérieur sont nécessaires pour atténuer les contraintes internes. Des exigences plus détaillées concernant le surfaçage sont décrites dans la documentation relative aux électrodes de surfaçage appliquées. Par exemple, les caractéristiques technologiques suivantes sont données pour l’électrode OZI-3: "Le revêtement est produit en une à quatre couches avec préchauffage à une température de 300 à 600 ° C. ° C, 1 h. "
La surface de la pièce est nettoyée de l'huile, de la rouille et de tout autre contaminant avant d'être recouverte.
Il existe différents systèmes pour la localisation des soudures. Dans le cas de surfaces planes, il existe deux types principaux de surfaçage: l'utilisation de rouleaux étroits se chevauchant de 0,3 à 0,4 mm de largeur et larges, obtenus par des mouvements transversaux accrus de l'électrode par rapport au sens de passage.
Une autre méthode consiste à poser des rouleaux étroits à une certaine distance les uns des autres. Lorsque ce laitier est retiré après l’imposition de plusieurs rouleaux. Après cela, les rouleaux sont soudés et dans les interstices.
Afin d'éviter toute déformation des pièces, il est recommandé d'effectuer le soudage en sections séparées, "de manière aléatoire", et de commencer la pose de chaque rouleau suivant du côté opposé par rapport au précédent.
Le surfaçage d'une surface cylindrique s'effectue de trois manières: des rouleaux le long du cylindre du générateur, des rouleaux sur des cercles fermés et le long d'une hélice. Cette dernière option (le long d'une ligne hélicoïdale) est particulièrement pratique dans le cas d'un surfaçage mécanisé, dans lequel les pièces pendant le processus de surfaçage sont soumises à une rotation uniforme.
Pour restaurer et augmenter la durée de vie des outils de coupe, de matrice et de mesure, ainsi que de parties de mécanismes fonctionnant sous une usure intense, on utilise le surfaçage de surfaces de travail en alliages durs, composés de métaux tels que titane, tungstène, tantale, manganèse, chrome et autres avec du bore , carbone, cobalt, fer, nickel, etc.
Dans la fabrication de nouveaux outils et de nouvelles pièces avec un revêtement en alliage dur, des pièces en acier au carbone ou en acier allié sont utilisées comme ébauches (bases). Dans le cas de réparation de pièces présentant une usure importante, avant le surfaçage avec des alliages durs, le pré-surfaçage est effectué avec des électrodes en acier à faible teneur en carbone.
Pour obtenir un surfaçage de qualité supérieure, éviter les fissures et réduire les contraintes, il est souvent recommandé de chauffer les pièces à une température de 300 ° C et plus.
Revêtement des outils de coupe et des matrices. Les outils de coupe de métal et les matrices travaillant avec l'estampage à froid et à chaud sont fondus avec des électrodes OZI-3, OZI-5, OZI-6, TsS-1, TsI-1M et d'autres marques. Le métal déposé par ces électrodes présente une résistance élevée à l'abrasion et à l'affaissement sous des charges spécifiques élevées et à des températures élevées allant jusqu'à 650-850 ° C. La dureté de la couche déposée sans traitement thermique varie de 52 HRC (OZI-5) à 61 HRC (OZI-3). 1-3 couches sont déposées avec une épaisseur totale de 2-6 mm. Avant le surfaçage, la pièce est chauffée à une température de 300-700 ° C (en fonction du type d'électrode).
Revêtement de pièces travaillant à l'abrasion sans choc. Si vous souhaitez obtenir un métal de soudure de dureté particulièrement élevée, vous pouvez utiliser des électrodes pour le surfaçage des T-590 et T-620. Ils sont spécifiquement conçus pour couvrir les pièces qui travaillent avec une abrasion intense. Leur noyau est en acier doux, mais les revêtements comprennent du ferrochrome, du ferrotitane, du ferrobore, du carbure de bore et du graphite. Grâce à ces matériaux, la dureté du métal soudé peut atteindre 62 à 64 unités HRC.
En raison du fait que le métal déposé est fragile et sujet à la fissuration, les produits, construits avec les électrodes T-590 et T-620, ne sont pas conçus pour fonctionner dans des conditions de chocs importants. Le surfaçage du métal de carbure est fait dans une ou deux couches. Si vous souhaitez souder une grande épaisseur, les couches inférieures sont déposées avec des électrodes en acier doux et uniquement les dernières - en carbure.
Revêtement de pièces abrasives soumises à des chocs. Les pièces en acier au manganèse (110G13L et similaires), fonctionnant dans des conditions d'usure de surface intense et de charges d'impact élevées (en particulier corps de construction et d'engins de terrassement), sont déposées avec des électrodes OMG-N, TsNIIN-4, OZN-7M, OZN-400M , OZN-300M et d’autres marques. Lors de leur utilisation, la dureté du métal déposé dans la deuxième couche est de 45 à 65 HRC avec des valeurs de viscosité élevées.
Surface en acier inoxydable. TsN-6L, TsN-12M-67 et d’autres marques sont utilisés pour le surfaçage des électrodes en acier inoxydable. Le noyau de ces électrodes est constitué de fil inoxydable fortement allié. En plus de sa grande résistance à la corrosion, le métal fondu présente également une résistance à la déchirure, ce qui permet d'utiliser ces électrodes pour surfacer des surfaces d'étanchéité dans des produits de renforcement.
Lors de l'utilisation d'électrodes pour le surfaçage d'aciers inoxydables, il est recommandé d'effectuer un chauffage préliminaire et concomitant de la pièce à une température de 300 à 600 ° C et de procéder à un traitement thermique après surfaçage.
Revêtement de cuivre et de ses alliages. Le surfaçage du cuivre et de ses alliages (bronze) peut être réalisé non seulement sur une base de cuivre ou de bronze, mais également sur de l'acier et de la fonte. Dans ce cas, il est créé des produits bimétalliques qui présentent les qualités de performances nécessaires (résistance élevée à la corrosion, faible coefficient de frottement et autres propriétés intéressantes inhérentes au cuivre et à ses alliages) et dont le coût est nettement inférieur à celui de pièces entièrement en cuivre. alliages.
Les bronzes en aluminium, en particulier, qui possèdent des propriétés antifriction élevées, fonctionnent très bien dans les unités de friction. Ils sont donc soudés sur des roues à vis sans fin, des craquelins et autres pièces fonctionnant dans des conditions de friction.
Le surfaçage de pièces en cuivre techniquement pur peut être réalisé avec des électrodes Komsomolets-100 ou en soudant des baguettes en cuivre ou ses alliages. Lors du surfaçage cuivre sur cuivre, le préchauffage est appliqué à une température de 300-500 ° C.
La couche déposée doit être de préférence forgée à une température de cuivre supérieure à 500 ° C.
Si un revêtement de bronze est nécessaire, vous pouvez utiliser des électrodes OZB-2M contenant, outre le composant en cuivre, de l'étain, du manganèse, du nickel et du fer. Les produits déposés avec des électrodes OZB-2M ont une résistance à l'usure superficielle élevée.
Le surfaçage du cuivre et de ses alliages se fait par courant continu de polarité inverse en position basse.
Revêtement en gaz protecteur
En plus des électrodes enrobées, à la maison, vous pouvez également souder des gaz de protection en utilisant la méthode MIG / MAG (avec alimentation automatique du fil) ou TIG (électrode en tungstène) avec des tiges de remplissage. Différents gaz peuvent être utilisés à des fins de protection: argon, dioxyde de carbone, hélium et azote, en fonction du métal déposé.Lors de la restauration des pièces en acier au carbone par soudage, du dioxyde de carbone moins coûteux peut être utilisé. Étant donné que le CO 2 oxyde le métal en fusion, le fil de remplissage doit dans ce cas contenir des désoxydants (manganèse, silicium, etc.).
Le surfaçage du cuivre et de ses alliages peut être réalisé sous azote neutre au cuivre.
Les aciers fortement alliés, les alliages à base de magnésium et d'aluminium sont fondus dans l'argon, l'hélium ou un mélange de ceux-ci.
L'électrode de tungstène non consommable de la gaine est réalisée en argon et en hélium. Général gaz inertesen particulier, l'argon, sont universels et conviennent au soudage et au surfaçage de presque tous les métaux.
Comme matériaux de soudage, on utilise des aciers au carbone semi-automatiques et des aciers faiblement alliés fil de soudure section continue (Sv-08GS, Sv-08G2S, Sv-12GS) et revêtement de surface spécial (Np-40, Np-50, Np-30HGSA). Pour surfacer le fil en acier inoxydable est utilisé en acier inoxydable. Le surfaçage peut être réalisé avec un fil fourré, ce qui permet d'obtenir une couche de soudure avec des propriétés spéciales.
Lors de la restauration de pièces par soudage, on utilise la méthode MIG / MAG comme dans le cas du MMA. courant continu inverser la polarité, fournissant moins de pénétration du métal de base. Lors de l'utilisation électrode de tungstène (Méthode TIG), utilisez la polarité directe, en éliminant la fusion de l'électrode en tungstène. Le surfaçage doit être aussi bref que possible afin d'éviter les éclaboussures de métal.
Lorsque vous utilisez le contenu de ce site, vous devez placer des liens actifs vers ce site, visibles pour les utilisateurs et les robots de recherche.