Електроди за напластяване, устойчиви на абразивно износване
Това един от най-простите и същевременно ефективни начини позволява не само да се възстанови пригодността (производителността) на частите. Чрез заваряване на метал с електрод можете да промените формата на пробата, да придадете други (различни от оригиналните) свойства на повърхностния слой, да увеличите неговата якост и устойчивост на износване. Каква е тази технология, какви са нейните характеристики и дали е възможно тя да бъде приложена в ежедневието - предмет на обсъждане в тази статия.
- Малко вероятно е читателят да се интересува от индустриални технологии, и дори с използването на роботизирани технологии, следователно, по-нататъшен акцент е върху техниката на заваряване на метали с електроди на ниво домакинство, т.е. със собствените си ръце.
- Често сплавите, например стоманата, също често се наричат метали. И двете технологии и отделните части (например марката електрод) за всеки конкретен случай могат да се различават леко. В една статия е невъзможно да се покрият буквално всички нюанси, така че преди да пристъпите към настилката, трябва да изясните някои точки относно използваните метали. Всичко, което е отбелязано по-долу, са само общи препоръки, както и самата заявка, въведена в низът на търсачката.
- Тъй като настилката е донякъде подобна на добре познатата заварка, ще бъде полезно да се прочетат статиите за технологията на последното във връзка с различни метали и сплави - мед, алуминий, чугун, неръждаема стомана и няколко други, в зависимост от спецификата на работата, която трябва да се извърши.
терминология
- Напластяване - свързването на различни метали чрез нанасяне на една повърхност на друга.
- Запълващ метал - който се прилага; по този метод основната се обработва повърхностно.
технология
Взаимното проникване на материалите става на молекулярно ниво. За тази цел повърхностният слой на субстрата се нагрява до стопилка до малка дълбочина и добавката се нагрява до течно състояние. Такава връзка се нарича хомогенна (от думата смесване, преведена от английски) и се характеризира с повишена надеждност, тъй като е невъзможно да се раздели на оригинални „части” с механични средства.
Предимствата на тази технология са възможностите за регулиране на дебелината на слоя (и в значителни граници) и прилагане на добавката към части (образци) от всякаква форма.
Основни плаващи правила
- Дълбочината на стопилката на горния слой на основата трябва да бъде възможно най-малка. Един от начините да се изпълни това условие е да се наклони електродът. Тя се прави в посока, обратна на посоката на движението му. Минималното смесване на различни метали спомага за намаляване на остатъчните напрежения и елиминира възможните деформации в определени области.
- Излишната добавка усложнява по-нататъшната обработка на частите, изисква повече труд и време.
Технология на електрода
Задължително е да се направи предварителна подготовка на основния метал - стрипинг + обезмасляване.
Напластяването с електроди е най-разпространеният метод за получаване на хомогенен слой. Поради простотата на технологията тя се счита за съществена за употреба както в производството, така и в домашни условия. В зависимост от основния метал и преследваните цели се избира електрод с подходящо покритие. В зависимост от марката, полученият слой придобива необходимите характеристики. Фигура обяснява всичко добре.
Схема на свързване - директна или обратна. Последният вариант се използва по-често, като по-удобен. Напрежението е постоянно, следователно, "+" е върху покрития електрод.
Технологични характеристики
- Дебелината и формата на слоя зависи от напречното сечение на електрода.
- За да се осигури високо качество на заварката, напрежението и интензитетът на тока на дъгата трябва да бъдат минимални и това изисква точно съвпадение. С придобиването на практически опит, изпълнението на това условие не е особено трудно.
Какво трябва да знаете
- Увеличаването на напрежението води до факта, че "валякът" не расте във височина, а по ширина. Дължината на дъгата се увеличава.
- За всяка - собствена функция за приложение. Например, трябва ли да подгряваме базата? за нисколегирани стомани това често не се изисква. Какъв е режимът на охлаждане? Какво задаване на ток? Всички технологични нюанси на облицовката са отразени в документацията за специфични електроди.
- По-добро е качеството на настилката, колкото е по-висока температурата на отопление. На практика за всички сплави и метали минималната му стойност е + 300 ºС. Вкъщи ще ви трябва най-малко една малка фурна (например електрическа камерна пещ).
Окабеляване на шевове
За плоски повърхности
Тесни ролки. Те съответстват на около 1/3 припокриване.
Wide. Електродът се движи перпендикулярно на оста на поплавъка. Колебателни движения, тяхната конфигурация (честота, амплитуда) се избира въз основа на размерите на основата.
Комбинирана техника. Покритието е с тесни ролки, но те са разположени на малко по-малко разстояние от тяхната широчина. След отстраняване на основата от шлаките в такива кухини се прави следващият поплавък. В резултат - получаване на непрекъснат хомогенен слой.
За да получите по-добро покритие на основата с друг метал, трябва да започнете да положите следващия валяк от другата страна на детайла. Освен това, наслояването не е последователно, едно след друго, а на случаен принцип, след това в една област, след това в друга. Това ще предотврати частичната деформация на субстрата при прегряване.
За цилиндри
И трите метода са показани на фигурата.
Има още една технология за напластяване на метали с електроди - в защитна газообразна среда. В основата си тя е проста. Трудността е различна - ще трябва да закупите цилиндър и да го напълните с подходящ газ (аргон, хелий или други), в зависимост от вида на запълващия метал. Тази опция е по-подходяща за малка работилница. Да придобие газова бутилка за еднократна работа у дома едва ли е препоръчително. Следователно, тази технология не се разглежда в статията.
Авторът разглежда препоръките за избора на електроди и спецификата на тяхното използване излишно. Първо, цялата необходима информация се съдържа на опаковката. Второ, продавачът ще отговори на всички неясни въпроси. В специализирани точки мениджърите са добре запознати с тези теми и могат да дадат практически съвети.
Като правило, заварчиците постоянно трябва да се справят с различни видове стомана. В същото време, няма универсална марка електроди, способни да работят еднакво ефективно на различни видове стомана, а специалистите трябва да ги вземат предвид технически характеристики по време на работа с този или онзи метал.
Класификация на електрода
Електродите, предназначени за тях, са разделени на няколко групи със специфични параметри, свързани с легиращи компоненти от различни видове стомана. Изброяваме най-често срещаните видове електроди за напластяване на стомани и представяме техните характеристики.
- Заваръчните електроди са ниски въглеродна стомана с ниско съдържание на легиращи елементи. Такива марки стомана са високо устойчиви на абразивно износване и устойчиви на удар.
- Електроди, предназначени за заваряване на нисколегирани стомани с ниско съдържание на въглерод. Такива марки стомана са силно устойчиви на триене и заварка може да издържа на температури до 650 градуса.
- Електроди за заваряване на легирани и високолегирани въглеродни стомани. Слоят от метал, нанесен по време на заваряване, е устойчив на абразия и ударни натоварвания.
- Високоуглеродни легирани стомани, устойчиви на високо налягане. Електродите от тази група се използват за работа под високо налягане. Заваръчният шев е в състояние да издържа на температури до 850 градуса
- Тази група съдържа електроди за заваряване на аустенитни (неръждаеми) висококачествени стомани. Характеристиките на консумативите позволяват да се получи шев от неръждаема стомана по време на заваряване.
- Електроди за работа с топлоустойчиви стомани, способни да издържат на високи температури над 1000 градуса.
Всички гореописани видове електроди са предназначени както за промишлена, така и за домашна употреба.
Състав и структура на електродите
За да се получат качествата, необходими за ефективното заваряване на различни видове стомани, се избират електродни пръти от различни видове в съответствие с марките заварени метали.
Съставът и структурата на електродите до голяма степен определят ефективността на напластяването на дъгата и свойствата на нанесения метален слой.
В допълнение към елементите, които формират основата на заваръчния метал, съставът на консумативите се допълва от добавки, които подобряват и улесняват процеса на заваряване. И така, електродите от марката UONI 1345 съдържат следните елементи:
- манган
- въглероден
- силиций
- фосфор
Но електродите на марката OZN 6, предназначени за заваряване на топлоустойчиви стомани, съдържат в състава си значителна част от титана, което гарантира правилното качество на настилката.
Класове електроди, предназначени за напластяване на стомани
Представете си най-разпространената марка електроди за заваряване на различни стомани.
- OZN 300M - за заваряване на компоненти и части от нисколегирана стомана, подложени на бързо износване.
- UON и 13NZh 20H13 - предназначени за напластяване на топлоустойчиви стомани, които могат да издържат на температури до 400 градуса.
- OZN 7 - електроди за заваряване на високо натоварени конструкции и елементи.
- T 590 - за заваръчни конструкции и части от високоуглеродисти стомани, които не са обект на големи натоварвания.
- OZI 5 - напластяване на износен слой металорежещи инструменти и форми за горещо щамповане
- OZSH 6 - ремонт на ковашко оборудване, машини и компоненти, работещи в условия на високи натоварвания и екстремни температури.
Избор на електроди за настилка от различни видове стомана
При избора на консумативи за заваряване е необходимо да се вземе предвид марката и структурата на заварената стомана, както и размерите на заготовките. Така за заваряване на големи, дебели части е необходимо да се изберат електроди от по-голяма секция, което ще позволи стоманата да се разтопи до достатъчна дълбочина за надеждна връзка. Освен това електродите с по-голям диаметър могат да издържат на големи токови натоварвания.
В момента, освен основните марки, има много аналози на производството на местни и чуждестранни компании. За да се избере оптималният вариант, е необходимо да се проучат подробно свойствата на консумативите и, доколкото е възможно, да се свържат с свойствата на заварените метали.
Обща кратка характеристика и каталог на електродите за напластяване.
Групата електроди за напластяване включва маркировки, предназначени за ръчно електродъгово заваряване на повърхностни слоеве със специални свойства (с изключение на маркировките за напластяване на слоеве от цветни метали). Те се произвеждат и доставят в съответствие с изискванията на ГОСТ 9466-75 и ГОСТ 10051-75. В някои случаи се използва и настилка. заваръчни електродиНапример, класове, предназначени за заваряване на високолегирани устойчиви на корозия, топлоустойчиви и топлоустойчиви стомани.
Съгласно ГОСТ 10051-75 електродите за напластяване на повърхностните слоеве се класифицират в 44 вида по химичен състав на заваръчния метал и твърдост при нормална температура (например, марки от тип E-16G2HM, E-110X14V13F2, E-13X16N8M5S5G46). Металът на заварка от много класове се регулира от спецификациите на производителите.
В зависимост от приетата допингова система и работните условия на получения заваръчен метал, електродите за напластяване (напластяващи електроди) могат да се разделят произволно на следните 6 групи:
Групата електроди за настилка е представена с маркировки, които са предназначени за ръчно напластяване на повърхностни слоеве на износени детайли. Такъв заварен слой има специални свойства (с изключение на видовете електроди, предназначени за заваряване на части от цветни метали). Електродите се произвеждат и доставят в съответствие с изискванията на ГОСТ 9466-75 и 10051-75.
В някои случаи за заваръчни работи се използват и заваръчни електроди, например марки, които са предназначени за заваряване и топлоустойчиви стомани.
Повърхностните електроди за възстановяване на повърхностните слоеве по ГОСТ 10051-75 според твърдостта и химичния състав на нанесения метал при нормална температура са разделени на 44 вида (например, Е-13Х16Н8М5С5Г46, Е-110Х14В13Ф2, Е-16Г2ХМ). Производителите на много марки регулират заваръчния метал с технически условия.
Условно разделение на групи
В зависимост от работните условия и приетата допингова система на получения заваръчен метал, заваръчните електроди (заваръчни електроди) са условно разделени на следните 6 групи: (Например, по-долу са марки / видове електроди (видове метал), връзките към всички тези марки са по-нататък на тази страница):
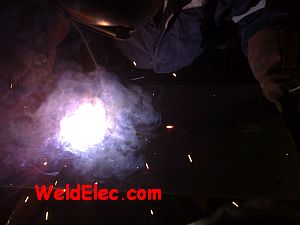
Електроди за напластяване, устойчиви на абразивно износване
Напластяването е метод за нанасяне на сърцевината на слой от разтопен метал, напълващ метал. Електродите за заваряване, устойчиви на износване, създават нов слой върху частите с отлични механични свойства и характеристики. Поради тяхната употреба можете:
- привеждане на продукта в първоначален вид,
- върнете го към геометричните размери
- дават нови ценни качества
- повишаване на износоустойчивостта, способност да издържа на въздействието на температурите.
Извършването на земни работи, връзките на веригите на гъсениците, кофите за багери, булдозерни ножове, върховете на рипърите са подложени на абразия. Защитете тези части от натоварване и разрушаване, като нанесете марката на електрода и. Техният прът е изработен от въглеродна стомана, мазилката съдържа феробор, бор карбид, ферохром, феротитан.
Удароустойчиви електроди за настилка
Електроди за напластяване, устойчиви на ударни натоварвания, се използват при ремонт на трошачно оборудване, като кърлежи, хапки, броня и ролки, конуси, сгради. Такива марки се използват, както го наричат ОК 86.08, Т-590 и Т-620. С тях можете да заварявате четири или повече слоя. T-590N е предназначен за тези, които са решили да поправят частта и да я забравят дълго време.
Марки Т-590 и Т-620 заваръчен слой, който не е подложен на образуване на пукнатини при удар. Те са износоустойчивТе са добре свързани с основния метал, спомагат за удължаване на експлоатационния живот на продуктите няколко пъти.
Твърдосплавни електроди
Твърдосплавни електроди, използвани за настилка, помагат за възстановяването на геометрията на много типове части. Добре подхождащи марки и ESAB OK 84.42 (прекратено) за нелегирана стомана. Възможно е да се заваряват продукти, изработени от карбидни стомани, изложени на абразивни и ударни ефекти, използвайки UTP PUR 600, ESAB OK 83.53 (Преустановени), Те са подходящи и за възстановяване на режещия измервателен уред, механизми, работещи при високо износване.
Слоят от метал, заварен с помощта на тръбен маркер, не може да бъде обработен. С твърдите сплави ви позволява да работите успешно. С тяхна помощ поправете повърхността на релсите, ножовете, кофите. Те имат висока твърдост от 55-63 HRC. Те са с диаметър 3,2-12 милиметра.
Удобства за заваряване на някои марки
ZELLER L61, Виж също клипса, където е демонстрирано отлагането с ZELLER L61 електрод.
Акценти на електродите за настилка
ВАЖНО! Заваръчен метален слой химични свойствасъставът на електрода трябва почти напълно да съвпада с характеристиките на стоманата на ремонтираната част. Това е важно да се има предвид при избора на марка, тип.
Принципът на действие на метода на отлагане се основава на топенето на електрода под влиянието на заваряване дъга, при създаването на един или повече слоеве. Колко от тях ще са необходими, за да се определи, като се обърне внимание на свойствата на детайла, в зависимост от изискванията.
В зависимост от дълбочината на проникване на метала се постигат добри качествени характеристики, създадени от заваръчния слой. Този индикатор трябва да бъде минимален. Важно е да се има предвид, че трябва да постигнете възможно най-малко смесване на стоманата, която се депонира с основната. Заварчикът трябва да се опита да постигне минималното остатъчно напрежение и да избегне деформацията на детайла. Това изискване може да бъде изпълнено само при спазване на предходните две, избора на правото електрод и минимално кипене.
Важно е да се намалят допустимите стойности, които са допустими при последваща обработка на детайли след заваряване, без да се надвишават.
За да се премахне изкривяването, настилката се прави най-добре в отделни секции и е препоръчително всеки следващ валяк да се полага от противоположната страна спрямо предишната.
Само чрез спазването на тези прости правила се защитава металът, който се отлага срещу вредните въздействия на газовете. Оказва се, че е плътна, без да има пори, всякакви видове пукнатини и слой от чужди включвания. Важно е да се вземе под внимание фактът, че повърхността на ремонтираната част трябва да се почисти старателно от масло, корозия, ръжда и всякакви други замърсявания преди започване на работа по настилката.
видео
Гледайте видеото, където майсторът изгражда оранжерия:
Тези, които използват различни механизми, понякога трябва да се сблъскат с необходимостта от заваряване на метал в определено детайлно място. Счупен монтажен отвор, износена повърхност по време на работа, разкъсан ръб на металорежещи инструменти, износен лагерна втулка. Във всички тези случаи можете да го направите, без да подменяте детайла, възстановявайки го по метода на металната настилка върху износената част. Напластяването върху метална част позволява не само да се възстановят оригиналните свойства на продукта, но и да му се придадат изцяло нови ценни качества. По-специално, чрез заваряване на слой от карбиден метал върху основата на нисковъглеродна стомана, може да се получи износоустойчив инструмент или режещ инструмент.
Повърхността е процес на нанасяне на един разтопен метал (наречен добавка) на повърхността на друг (наречен основен). В същото време основният метал също се разтопява до малка дълбочина, за да образува хомогенно съединение. Целта на настилката може да бъде различна: възстановяване на загубената геометрия на детайла или придаване на нова форма, образуване на повърхностен слой с желани физични и механични свойства (като повишена твърдост, износоустойчивост, антифрикционна устойчивост, устойчивост на топлина и др.), Втвърдяване чрез заваряване.
Напластяването може да се извърши върху всякаква повърхност - плоска, заострена, цилиндрична, сферична. В големи граници дебелината му може да варира от няколко милиметра до сантиметри или повече.
Основни принципи на настилка
В основните си точки, технологията на отлагане е подобна на технологията на заваряване. Той е изправен пред същите задачи, както преди заваряване - защита на метала, който се отлага от газове, съдържащи се във въздуха, като се получават плътни, без пори, пукнатини и чужди включвания на заваръчния метал. Затова е важно да се запознаете с общата статия за заваряване, предмети за заваряване на съответните метали (заваряване на мед, заваряване от чугун, заваряване от алуминий, заваряване от неръждаема стомана) и електродни покрития, в противен случай няма да има разбиране, например, защо калцираме електродите преди настилката и какви последствия не го правете, или защо полярността на връзката с електрода е важна, При настилката е необходимо да се следват основните принципи, съдържащи се в редица изисквания:- Необходимо е да се стремим към минимално проникване на основния метал. Това се постига чрез накланяне на електрода в посока, противоположна на отлагането.
- Трябва да има възможно най-малко смесване на заваръчния метал с основния.
- Трябва да се опитаме да постигнем минимални остатъчни напрежения и деформации в частите. Това изискване до голяма степен се осигурява от спазването на предходните две.
- Необходимо е да се намалят допустимите стойности на допустимите стойности за последващата обработка на детайла. С други думи, трябва да заварявате метал точно толкова, колкото е необходимо, и не повече.
Прилагат се различни методи за напластяване на метали - електрическа дъга, газ, електрошлакова, индукционна, плазмена, импулсна дъга, вибрационна дъга, прахово напластяване. Най-широко разпространената дъга.
Материали за настилка съществуват в различни форми. Това могат да бъдат пълнители, прахови смеси, покрити с покритие електроди, както и пълнене и плътен проводник. При напластяване с електрическа дъга се използват главно покрити електроди, пълнители и проводници.
Напластяване с покрити електроди
Покриването с покрити електроди се отнася до основните методи, използвани както в промишлеността, така и в ежедневието, поради простотата, удобството и липсата на необходимост от специално оборудване. Произвеждат се голям брой електроди, които създават покривен слой с различни характеристики, които осигуряват необходимите качества на продуктите за работа при определени условия.Покриването изисква определени умения в работата. Необходимо е при минимален ток и напрежение, за да не се увеличава делът на основния метал в заваръчния метал, за да се разтопят двата компонента. Съставът на метала ще определи вида на електрода, а дебелината и формата - диаметърът на електрода. Напрежението на дъгата определя формата на заваръчния шев, като се увеличава, ширината се увеличава и височината на валяка намалява, дължината на дъгата и окисляемостта на добавките, особено на въглерода, се увеличават. В тази връзка, са склонни към минималното напрежение, което трябва да бъде в съответствие с дъга ток.
Напластяването на детайли от стомана се извършва по правило с постоянен ток. обратна полярност (на електрода "плюс") в долната позиция.
Части от нисковъглеродни и нисколегирани стомани обикновено се отлагат без предварително загряване. Но често се изисква предварително загряване и последваща топлинна обработка, за да се облекчат вътрешните напрежения. По-подробни изисквания за настилка са дадени в документацията за използваните електроди за напластяване. Например, за електрода OZI-3 са предвидени следните технологични характеристики: "Покритието се произвежда от един до четири слоя с предварително загряване до температура от 300-600 ° C. Следващото охлаждане се препоръчва след напластяване. Възможно е заваряване при висока температура. ° С, 1 час. "
Повърхността на детайла се почиства от масло, ръжда и други замърсители преди покриването.
Съществуват различни схеми за разположението на заваръчните шевове. В случая на плоски повърхности, има два основни вида настилка - използването на тесни ролки с припокриване една с друга с 0,3-0,4 от тяхната широчина и широки, получени чрез увеличени напречни движения на електрода спрямо посоката на преминаване.
Друг начин - полагане на тесни ролки на известно разстояние един от друг. Когато тази шлака се отстранява след нанасянето на няколко ролки. След това валовете са заварени и в пролуките.
За да се избегне изкривяване на частите, препоръчва се заваряването да се извършва в отделни секции, "случайно", и полагането на всеки следващ валяк да се започва от противоположната страна спрямо предишната.
Напластяването на цилиндрична повърхност се извършва по три начина - валяци по генератора на цилиндъра, ролки върху затворени кръгове и по спирала. Последната опция (по спирална линия) е особено удобна в случай на механизирано напластяване, при което частите по време на процеса на напластяване получават еднакво въртене.
За възстановяване и увеличаване на експлоатационния живот на режещите, щанцовите и измервателните инструменти, както и на части от механизми, работещи при интензивно износване, се използва напластяване на работни повърхности с твърди сплави, които са съединения на метали като титан, волфрам, тантал, манган, хром и др. въглерод, кобалт, желязо, никел и др.
При производството на нови инструменти и части с твърда сплав, като заготовки (основи) се използват части от въглеродни или легирани стомани. В случай на ремонт на части с голямо износване, преди напластяване с твърди сплави, предварително настилка се извършва с нисковъглеродни стоманени електроди.
За да се постигне по-високо качество на настилката, да се предотврати напукването и да се намали напрежението, в много случаи е препоръчително обработваните детайли да се загреят до температура от 300 ° C и по-висока.
Нанасяне на метални режещи инструменти и матрици, Металорежещите инструменти и матрици, работещи със студено и горещо щамповане, са покрити с електроди ОЗИ-3, ОЗИ-5, ОЗИ-6, ЦС-1, ЦИ-1М и други марки. Металът, нанесен от тези електроди, има висока устойчивост на абразия и срутване при високи специфични натоварвания и високи температури - до 650-850 ° С. Твърдостта на отложения слой без топлинна обработка варира от 52 HRC (OZI-5) до 61 HRC (OZI-3). 1-3 слоя се отлагат с обща дебелина 2-6 мм. Преди настилката детайлът се загрява до температура 300-700 ° С (в зависимост от вида на електрода).
Напластяване на части, които работят на абразия без ударни натоварвания, Ако искате да получите наварен метал с особено висока твърдост, можете да използвате електроди за напластяване T-590 и T-620. Те са специално проектирани за покриване на части, които работят с интензивна абразия. Тяхната сърцевина е изработена от мека стомана, но покритията включват ферохром, феротитан, феробор, бор карбид и графит. Благодарение на тези материали, твърдостта на заваръчния метал може да достигне 62-64 HRC единици.
Поради факта, че депонираният метал е крехък и склонен към напукване, продуктите, изградени с електроди Т-590 и Т-620, не са предназначени за работа в условия на значителни ударни натоварвания. Напластяването на карбидния метал се извършва в един или два слоя. Ако искате да заварявате голяма дебелина, долните слоеве се нанасят с електроди от мека стомана, а само крайните - с карбид.
Напластяване на абразивни части с удари, Части, изработени от манганови стомани (110G13L и др.), Работещи в условия на интензивно износване на повърхността и силни ударни натоварвания (по-специално работни тела на строителна и земна техника), се отлагат с електроди OMG-N, ЦНИИН-4, ОЗН-7М, ОЗН-400М , OZN-300M и други марки. При използването им твърдостта на отложения метал във втория слой е 45-65 HRC с високи стойности на вискозитета.
Покритие от неръждаема стомана, За покриване на части от неръждаема стомана се използват ТСН-6Л, ЦН-12М-67 и други марки. Ядрото на тези електроди е изработено от високолегиран неръждаем тел. В допълнение към високата устойчивост на корозия, металът на заварка също има устойчивост на разкъсване, което прави възможно използването на тези електроди за напластяване на уплътнителни повърхности в армировъчните продукти.
Когато се използват някои електроди за напластяване на неръждаеми стомани, се препоръчва да се извърши предварително и съпътстващо нагряване на детайла до температура от 300-600 ° C и да се извърши топлинна обработка след настилка.
Покритие на мед и неговите сплави, Напластяването на мед и неговите сплави (бронз) може да се извършва не само върху медна или бронзова основа, но и върху стомана и чугун. В този случай се създават биметални продукти, които имат необходимите експлоатационни качества (висока устойчивост на корозия, нисък коефициент на триене и други ценни свойства, присъщи на медта и неговите сплави) и имат много по-ниска цена в сравнение с частите, изработени изцяло от мед или сплави.
Алуминиевите бронзи, особено притежаващи високи антифрикционни свойства, работят много добре в триещи единици, следователно те се заваряват върху червячни колела, бисквити и други части, работещи при условия на триене.
Напластяването на части от технически чиста мед може да се направи от електроди Комсомолец-100 или чрез заваръчни пръти от мед или негови сплави. При напластяване на мед върху мед, загряването се извършва при температура от 300-500 ° С.
За предпочитане е депозираният слой да бъде кован при температура на медта над 500 ° С.
Ако се изисква настилка с бронз, могат да се използват OZB-2M електроди, които освен медния компонент съдържат калай, манган, никел и желязо. Продукти, наслоени с електроди OZB-2M, имат висока устойчивост на износване на повърхността.
Покриването на мед и неговите сплави се извършва чрез постоянен ток на обратната полярност в долното положение.
Напластяване на защитен газ
Заедно с покрити електроди, в дома, можете също да заварявате в защитни газове с помощта на метода MIG / MAG (с автоматизирано подаване на тел) или TIG (волфрамов електрод) с пълнители. За защита могат да се използват различни газове: аргон, въглероден диоксид, хелий и азот, в зависимост от депонирания метал.При възстановяване на частите от въглеродна стомана чрез заваряване може да се използва по-евтин въглероден диоксид. Предвид факта, че CO 2 окислява разтопения метал, запълващата тел в този случай трябва да има дезоксидиращи вещества (манган, силиций и др.).
Напластяването на мед и неговите сплави може да се извърши в азот, който е неутрален към мед.
Високолегираните стомани, магнезиевите и алуминиевите сплави са разтопени в аргон, хелий или смес от тях.
Облицовъчният неопитен волфрамов електрод се извършва в аргон и хелий. като цяло, инертни газовеособено аргон, са универсални, подходящи за заваряване и напластяване на почти всеки метал.
Като материали за заваряване се използват полуавтоматични въглеродни и нисколегирани стомани заваръчна тел непрекъсната секция (Sv-08GS, Sv-08G2S, Sv-12GS) и специална настилка (Np-40, Np-50, Np-30HGSA). За покритие от неръждаема стомана се използва неръждаема стомана. Напластяването може да се извърши с тел с флуидна сърцевина, който позволява да се получи слой на заварка със специални свойства.
При възстановяване на части чрез заваряване се използва методът MIG / MAG, както при MMA постоянен ток обратна полярност, осигуряваща по-малко проникване на основния метал. Когато използвате волфрамов електрод (TIG метод) използва директна полярност, елиминирайки разтопяването на волфрамовия електрод. Повърхността трябва да се опитва да бъде възможно най-кратка - за да се избегне пръскането на метал.
Когато използвате съдържанието на този сайт, трябва да поставите активни връзки към този сайт, видими от потребителите и търсещите роботи.