Електроди для наплавлення, стійкі до абразивного зносу
Цей один з найбільш простих, і в той же час ефективних способів дозволяє не тільки відновлювати придатність (працездатність) деталей. Наплавленням металу електродом можна змінити форму зразка, надати поверхневому шару інші (відмінні від початкових) властивості, підвищити його міцність і зносостійкість. У чому полягає така технологія, які її особливості та чи можлива реалізація в побуті - предмет розгляду в цій статті.
- Читача навряд чи цікавлять промислові технології, та ще й з використанням роботизованої техніки, тому далі акцент - саме на методиці наплавлення металів за допомогою електродів на побутовому рівні, тобто своїми руками.
- Часто в побуті металами називають і сплави, наприклад, сталь. І технології, і окремі деталі (наприклад, марка електрода) для кожного конкретного випадку можуть дещо відрізнятися. В одній статті неможливо охопити буквально всі нюанси, тому перед тим, як приступити до наплавленні, слід уточнити окремі моменти, що стосуються використовуваних металів. Все, що відзначено нижче - лише рекомендації загального характеру, так само, як і сам запит, введений в рядок пошуковика.
- Так як наплавка в чомусь схожа з відомою всім зварюванням, корисно буде почитати статті по технології останньої стосовно різних металів і сплавів - міді, алюмінію, чавуну, нержавійці і ряду інших, в залежності від специфіки майбутньої роботи.
Термінологія
- Наплавлення - з'єднання різнорідних металів способом нанесення одного на поверхню іншого.
- Присадний метал - який наноситься; основний - піддається поверхневої обробки за такою методикою.
технологія
Взаємне проникнення матеріалів відбувається на молекулярному рівні. Для цього поверхневий шар основи розігрівається до розплавлення на невелику глибину, а присадка - до переходу в рідкий стан. Таке з'єднання називається гомогенним (від слова змішування, в перекладі з англійської) і відрізняється підвищеною надійністю, так як механічним шляхом розділити його на вихідні «частини» неможливо.
Перевагами такої технології є можливості з регулювання товщини шару (причому в значних межах) і нанесення присадки на деталі (зразки) будь-якої форми.
Основні правила наплава
- Глибина розплаву верхнього шару основи повинна бути якомога менше. Один із способів, що дозволяють виконати цю умову - нахил електрода. Він робиться в сторону, протилежну напрямку його переміщення. Мінімальна перемішування різнорідних металів сприяє зниженню залишкових напруг і виключає можливі деформації на окремих ділянках.
- Надлишок присадки ускладнює подальшу обробку деталі, вимагає великих трудовитрат і часу.
Технологія наплава електродами
В обов'язковому порядку проводиться попередня підготовка металу основи - зачистка + знежирення.
Наплавлення електродами - найбільш поширений спосіб отримання гомогенного шару. Завдяки простоті технології вважається основним для застосування як на виробництві, так і в домашніх умовах. Залежно від металу основи і переслідуваних цілей підбирається електрод з відповідним наплавоч покриттям. Залежно від його марки одержуваний шар набуває необхідні характеристики. Малюнок все добре пояснює.
Підключення схеми - пряме або зворотне. Останній варіант використовується частіше, як більш зручний. Напруга - постійне, отже, «+» - на вкритому електроді.
особливості технології
- Товщина і форма шару залежать від перетину електрода.
- Для забезпечення якісного наплава напруга і сила струму дуги повинні бути мінімальними, а це вимагає точного узгодження. З придбанням практичного досвіду виконання даного умови особливих труднощів не представляє.
Що потрібно знати
- Підвищення напруги призводить до того, що «валик» зростає не в висоту, а в ширину. При цьому довжина дуги збільшується.
- Для кожного - своя особливість застосування. Наприклад, чи потрібен попередній нагрів основи? для низьколегованих сталей це часто не потрібно. В якому режимі проводиться охолодження? Який виставити струм? Всі технологічні нюанси наплавлення відображені в документації на конкретні електроди.
- Якість наплавлення тим краще, чим вище температура розігріву. Практично для всіх сплавів і металів її мінімальне значення + 300 ºС. У домашніх умовах знадобиться хоча б невелика термопечь (наприклад, електрична камерна).
Схеми наплавлювальних швів
Для поверхонь плоских
Вузькими валиками. Вони укладаються з перекриттям приблизно в ⅓ третину.
Широкими. Електрод переміщається перпендикулярно осі наплава. Рухи коливальні, їх конфігурація (частота, амплітуда) вибирається виходячи з габаритів основи.
Комбінована методика. Наплав проводиться валиками вузькими, але вони розташовуються на відстані, трохи меншому їх ширини. Після зачистки основи від шлаків в такі порожнечі проводиться черговий наплав. Як результат - отримання суцільного гомогенного шару.
Для отримання більш якісного покриття основи іншим металом потрібно починати укладання чергового валика з протилежного боку деталі. Причому накладати шари не послідовно, один за іншим, а врозкид - то на одній ділянці, то на іншому. Це охоронить основу від часткової деформації при перегріванні.
для циліндрів
Всі три способи показані на малюнку.
Є ще одна технологія наплавлення металів за допомогою електродів - в захисній газовому середовищі. За своєю суттю вона нескладна. Труднощі в іншому - доведеться купувати балон і заправляти його відповідним газом (аргоном, гелієм або іншим) в залежності від виду присадочного металу. Такий варіант більш підходить для невеликої майстерні. купувати ж газовий балон для разової роботи в домашніх умовах навряд чи доцільно. Тому дана технологія в статті не розглядається.
Давати рекомендації по вибору електродів і специфіці їх використання автор вважає зайвим. По-перше, вся необхідна інформація міститься на упаковці. По-друге, на всі незрозумілі питання відповість продавець. У спеціалізованих точках менеджери непогано орієнтуються в подібній тематиці і можуть дати ділову пораду.
Як правило, сварщикам постійно доводиться мати справу з різними марками сталі. При цьому якоїсь універсальної марки електродів, здатних однаково ефективно зварювати різні сорти стали не існує, і фахівцям необхідно враховувати їх технічні характеристики при роботі з тим чи іншим металом.
Класифікація електродів
Електроди, призначені для, підрозділяються на кілька груп, що мають певні параметри, що співвідносяться з легуючими складовими різних марок сталі. Перелічимо найбільш поширені типи електродів для наплавлення стали і представимо їх особливості.
- Електроди для зварювання низько вуглецевих сталей з низьким вмістом легуючих елементів. Подібні марки сталей відрізняються високою стійкістю до абразивного зносу і мають стійкість до ударних впливів.
- Електроди, призначені ля зварювання середньовуглецевих низьколегованих сталей. Такі марки сталей мають високу стійкість до тертя, а зварний шов здатний витримувати температуру до 650 градусів.
- Електроди для зварювання легованих і високолегованих вуглецевих сталей. Шар наплавленого при зварюванні металу має стійкість до абразивного впливу і ударних навантажень.
- високовуглецевих легованих сталей, стійких до високого тиску. Електроди цієї групи застосовуються для, що працюють під високим тиском. Наплав сталевого шва здатний витримувати температури до 850 градусо
- У цій групі представлені електроди для зварювання аустенітних (нержавіючих) високолегованих марок сталі. Характеристики витратних матеріалів дозволяють отримувати нержавіючий шов при зварюванні.
- Електроди для роботи з термостійкими марками сталі, здатними витримувати високі температури, що перевищують 1000 градусів.
Всі перераховані вище типи електродів призначені як для промислового, так і побутового застосування.
Склад і структура електродів
Для отримання якостей, необхідних для ефективної зварювання різних сортів сталей, стрижні електродів різних типів підбираються відповідно до марками підлягають зварюванню.
Склад і структура електродів багато в чому визначають ефективність дугового наплавлення і властивості наплавленого шару металу.
Крім елементів, що становлять основу зварюється, склад витратних матеріалів доповнюють присадки, що поліпшують і полегшують процес зварювання. Так, електроди марки УОНІ 1 345 містять такі елементи:
- марганець
- вуглець
- кремній
- фосфор
А ось електроди марки ОЗН 6, призначені для зварювання теплостійких сталей, містять в своєму складі значну частку титану, що забезпечує належну якість наплава.
Марки електродів, призначених для наплавлення сталей
Уявімо найбільш поширені марки електродів для наплавлення різних сталей.
- ОЗН 300М - використовується для зварювання вузлів і деталей з низьколегованих сталей, схильних до швидкого зносу.
- УОН і 13НЖ 20Х13 - призначені для наплавлення термостійких сталей, що витримують температуру до 400 градусів.
- ОЗН 7 - електроди для зварювання високонавантажених конструкцій і елементів.
- Т 590 - для зварювання конструкцій і деталей з високовуглецевих сталей, не схильних до високих навантажень.
- ОЗИ 5 - наплавка зношеного шару металорізальних інструментів і прес-форм гарячого штампування
- ОЗШ 6 - ремонт ковальсько-пресового устаткування, верстатів і вузлів, що працюють в умовах високих навантажень і екстремальних температур.
Вибір електродів для наплавлення різних марок сталі
При виборі витратних матеріалів для зварювання слід обов'язково враховувати марку і структуру стали, яку належить зварювати, а також розміри заготовок. Так, для зварювання великих, товстих деталей необхідно вибрати електроди більшого перетину, що дозволить розплавити сталь на достатню для надійного з'єднання глибину. Крім того, електроди більшого діаметру здатні витримувати високу струмовий навантаження.
В даний час, крім основних марок, представлено безліч аналогів виробництва вітчизняних і зарубіжних компаній. Для вибору оптимального варіанту необхідно детально вивчити властивостей витратних матеріалів і, по можливості максимально, співвіднести їх з властивостями металів, що зварюються.
Загальна коротка характеристика і каталог наплавлювальних електродів.
До групи електродів для наплавлення входять марки, призначені для ручного дугового наплавлення поверхневих шарів з особливими властивостями (крім марок для наплавлення шарів з кольорових металів). Їх виготовляють і поставляють відповідно до вимог ГОСТ 9466-75 і ГОСТ 10051-75. Для наплавних робіт в деяких випадках також використовують зварювальні електроди, Наприклад, марки, призначені для зварювання високолегованих корозійно -стійку, жаростійких і жароміцних сталей.
Згідно ГОСТ 10051-75 електроди для наплавки поверхневих шарів за хімічним складом наплавленого металу і твердості при нормальній температурі класифіковані на 44 типу (наприклад, марки типу Е-16Г2ХМ, Е-110Х14В13Ф2, Е-13Х16Н8М5С5Г46). Наплавлений метал багатьох марок регламентується технічними умовами підприємств-виробників.
Залежно від прийнятої системи легування і умов роботи одержуваного наплавленого металу електроди для наплавки (наплавочні елекіроди) можуть бути умовно розділені на наступні 6 груп:
Група електродів для наплавлення представлена марками, які призначені для ручної наплавлення поверхневих шарів зношених деталей. Такий наплавляється шар має особливі властивості (крім марок електродів призначених для наплавлення деталей з кольорових металів). Наплавляти електроди виготовляються і поставляються відповідно до вимог ГОСТів 9466-75 і 10051-75.
У деяких випадках для наплавочних робіт використовують також зварювальні електроди, такі марки, наприклад, які призначені для зварювання, і жаростійких сталей.
Наплавлювальні електроди для відновлення поверхневих шарів відповідно до Держстандарту 10051-75 по твердості і хімічним складом наплавляємого металу при нормальній температурі розподіляються на 44 типу (наприклад, Е-13Х16Н8М5С5Г46, Е-110Х14В13Ф2, Е-16Г2ХМ). Підприємства виробники багато марки регламентують наплавлений метал технічними умовами.
Умовний розподіл на групи
Залежно від умов роботи і прийнятої системи легування одержуваного наплавляємого металу наплавочні електроди (електроди для наплавки) умовно поділяються на 6 таких груп (Для прикладу нижче написані марки / типи електродів (типи металу), посилання на всі ці марки є далі, на цій сторінці):
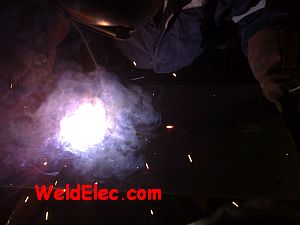
Електроди для наплавлення, стійкі до абразивного зносу
Наплавлення - це метод нанесення шару розплавленого металу, присадочного, на основний. Електроди для наплавлення, стійкі до абразивного впливу, створюють на деталях новий шар з відмінними механічними властивостями і характеристиками. За рахунок їх використання можна:
- привести виріб у первісний вигляд,
- повернути йому геометричні розміри,
- надати нові цінні якості,
- збільшити зносостійкість, здатність протистояти впливу температур.
Виконуючи земляні роботи, абразивного стирання піддаються ланки ланцюгів гусениць, ковші екскаваторів, ножі бульдозерів, наконечники розпушувачів. Захистити від навантажень і руйнування ці деталі необхідно застосовуючи марку електрода і,. Їх пруток зроблений з вуглецевої сталі, обмазка містить ферробор, карбід бору, ферохром, ферротитан.
Електроди для наплавлення, стійкі до ударних навантажень
Електроди для виконання робіт по наплавленні, стійкі до ударних навантажень, використовуються при ремонті дробильного обладнання, наприклад, кліщів, била, броні і роликів, конусів, корпусів. Застосовуються такі марки як, раніше її називали OK 86.08, Т-590 і Т-620. З їх допомогою можна наплавить чотири і більше шарів. Т-590Н розроблений для тих, хто вирішив відремонтувати деталь і надовго забути про неї.
Марки Т-590 і Т-620 наплавляют шар не схильний до утворення тріщин при ударі. вони зносостійкі, Добре з'єднуються з основним металом, допомагають продовжити ресурс роботи виробів у кілька разів.
Твердосплавні електроди для наплавки
Твердосплавні електроди, використовувані для наплавлення, допомагають відновити геометрію багатьох видів деталей. Добре підходять марки, і ESAB OK 84.42 (зняті з виробництва) для нелегованої сталі. Провести наплавку виробів, зроблених з твердосплавних сталей, що піддаються абразивному і ударної дії, можна використовуючи, UTP PUR 600, ESAB OK 83.53 (Зняті з виробництва). Вони підходять і для відновлення ріжучого вимірювального інструмента, механізмів, що працюють при високому знос.
Не підлягає механічній обробці шар металу, наплавлений при використанні електрода тубулярного марки. З твердими сплавами дозволяє успішно працювати,. З їх допомогою ремонтуються поверхні гусениць, різці, ковші. У них висока твердість 55-63 HRC. Вони бувають діаметром 3,2-12 міліметрів.
Особливості зварювання деякими марками
ZELLER L61. Подивіться також ролик, де продемонстрована наплавка електродом ZELLER L61.
Основні моменти по наплавленні електродами
ВАЖЛИВО! Наплавляється шар металу за хімічними властивостями, склад електрода, повинен практично повністю збігатися з характеристиками стали ремонтованої деталі. Це важливо врахувати при виборі марки, виду.
Принцип дії методу наплавлення заснований на плавленні електрода під впливом зварювальної дуги, На створенні одного або декількох шарів. Скільки їх буде, потрібно визначити, звернувши увагу на властивості деталі, в залежності від пропонованих вимог.
Хороші якісні характеристики створюваного зварювальником шару досягаються в залежності від глибини проплавлення металу. Цей показник повинен бути мінімальним. Це важливо врахувати, потрібно досягти наскільки можливо меншого перемішування наплавлюваного стали провідною. Зварювальник повинен намагатися отримати мінімальне залишкове напруга і уникати деформації оброблюваної їм деталі. Ця вимога можна виконати, тільки дотримуючись два попередніх, правильно вибравши електрод і мінімальним проварюванням.
Важливо знизити до встановлених нормою значення припуску, допустимі при подальшій після зварювання обробки деталей, що не перевищувати їх.
Щоб виключити викривлення, наплавление найкраще робити окремими ділянками, а укладку кожного наступного валика радиться починати з протилежного боку по відношенню до попереднього.
Тільки завдяки дотриманню цих простих правил досягається захист наплавляємого металу від руйнівного впливу газів. Виходить щільний, що не має часу, будь-яких видів тріщин і сторонніх включень шар. Важливо врахувати й те, що поверхня ремонтованої деталі перед початком виконання робіт по наплавленні необхідно ретельно очистити від масла, слідів корозії, іржі і будь-яких інших видів забруднень.
Відео
Подивіться ролик, де умілець наплавляє лемеші:
Тим, хто експлуатує різні механізми, доводиться іноді стикатися з необхідністю наплавить метал в тому чи іншому місці деталі. Розбите кріпильний отвір, стерта в процесі експлуатації поверхню, викришених кромка металорізального інструменту, зношена втулка підшипника. У всіх цих випадках можна обійтися без заміни деталі, відновивши її способом наплавлення металу на зношену частину. Наплавлення на деталь металу дозволяє не тільки відновити початкові властивості виробу, але і надати йому абсолютно нові цінні якості. Зокрема, наплаву на підставу з низьковуглецевої сталі шар твердосплавного металу, можна отримати зносостійкий робочий орган або ріжучий інструмент.
Наплавленням називається процес нанесення одного розплавленого металу (званого присадним) на поверхню іншого (званого основним). При цьому основний метал також розплавляється на невелику глибину для освіти гомогенного з'єднання. Мета наплавлення може бути різною: відновлення втраченої геометрії деталі або надання їй нової форми, утворення поверхневого шару з заданими фізико-механічними властивостями (такими як підвищена твердість, зносостійкість, антіфрікционность, корозійна стійкість, жаростійкість та ін.), Зміцнення наплавленням.
Наплавлення можна виробляти на будь-які поверхні - плоскі, конічні, циліндричні, сферичні. У великих межах може змінюватися і її товщина - від декількох часток міліметра до сантиметра і більше.
Основні принципи наплавлення
В основних своїх моментах технологія наплавлення подібна з технологією зварювання. Перед нею стоять ті ж завдання, що і перед зварюванням - захист наплавляємого металу від газів, що містяться в повітрі, отримання щільного, без пір, тріщин і сторонніх включень металу шва. Тому важливо ознайомитися із загальною статтею про зварювання , Зі статтями про зварювання відповідних металів ( зварювання міді , зварювання чавуну , зварювання алюмінію , зварювання нержавіючої сталі) та про покриття електродів , Інакше не буде розуміння, наприклад, навіщо прожарювати електроди перед наплавленням і які будуть наслідки якщо її не зробити, або чому важлива полярність підключення електроду. При наплавленні слід дотримуватися основних принципів, які полягають в ряді вимог:- Необхідно прагнути до мінімального проплавлению основного металу. Це досягається шляхом нахилу електрода в сторону, зворотну ходу наплавлення.
- Повинно бути якомога менше перемішування наплавленого металу з основним.
- Потрібно намагатися досягти мінімальних залишкових напруг і деформацій в деталі. Ця вимога багато в чому забезпечується дотриманням двох попередніх.
- Необхідно знижувати до прийнятних значень припуски на подальшу обробку деталі. Говорячи іншими словами, потрібно наплавляти металу рівно стільки, скільки необхідно, і не більше.
Застосовуються різні способи наплавлення металу - електродугове, газова, електрошлакове, індукційна, плазмова, імпульсно-дугова, вибродуговая, порошкова наплавлення. Найбільшого поширення набула дугове наплавлення.
Матеріали для наплавлення існують в різних формах. Це можуть бути присадочні прутки, порошкоподібні суміші, наплавочні покриті електроди, порошкова і цельностержневая дріт. У електродугової наплавленні застосовуються в основному покриті електроди, присадні прутки і дріт.
Наплавлення покритими електродами
Наплавлення покритими наплавоч електродами відноситься до основних способів, що застосовуються як в промисловості, так і в побуті, в силу її простоти, зручності, відсутності необхідності в спеціальному обладнанні. Випускається велика кількість марок електродів, що створюють наплавочні шар з різними характеристиками, що забезпечують необхідні якості виробів для роботи в тих чи інших умовах.Наплавлення вимагає певних навичок в роботі. Треба при мінімальному струмі і напрузі, щоб не збільшувати частку основного металу в наплавленому, оплавити обидва компонента. Склад металу буде визначати тип електрода, а товщину і форму - діаметр електрода. Напруга дуги визначає форму наплавленого валика, при його підвищенні збільшується ширина і зменшується висота валика, зростає довжина дуги і окислюваність легуючих домішок, особливо вуглецю. У зв'язку з цим прагнуть до мінімального напрузі, яке повинно узгоджуватися з струмом дуги.
Наплавлення деталей зі сталі здійснюється, як правило, на постійному струмі зворотної полярності (на електроді "плюс") в нижньому положенні.
Деталі з низьковуглецевих і низьколегованих сталей наплавляют зазвичай без попередньо нагрівання. Але нерідко потрібно попередній підігрів і подальша термообробка з метою зняття внутрішніх напружень. Більш детальні вимоги до наплавленні повідомляються в документації на застосовувані наплавочні електроди. Наприклад, для електрода ОЗИ-3 наводяться наступні технологічні особливості: "Наплавлення проводять в один-чотири шари з попереднім підігрівом до температури 300-600 ° С. Після наплавлення рекомендується повільне охолодження. Можлива наплавка ванним способом на підвищених режимах. Прокалке перед наплавленням: 350 ° С, 1 ч. "
Поверхня деталі перед наплавленням очищається від масла, іржі та інших забруднень.
Застосовуються різні схеми розташування наплавлювальних швів. У разі плоских поверхонь розрізняють два основних види наплавки - використання вузьких валиків з перекриттям один одного на 0,3-0,4 їх ширини, і широких, отриманих збільшеними поперечними рухами електрода щодо направлення проходу.
Інший спосіб - укладання вузьких валиків на деякій відстані один від іншого. При цьому шлак видаляють після накладення декількох валиків. Після цього валики наплавляються і в проміжках.
Щоб уникнути жолоблення деталей, наплавление рекомендується проводити окремими ділянками, "врозкид", а укладку кожного наступного валика починати з протилежного боку по відношенню до попереднього.
Наплавлення циліндричної поверхні виконується трьома способами - валиками вздовж твірної циліндра, валиками по замкнутим колах і по гвинтовій лінії. Останній варіант (по гвинтовий лінії) є особливо зручним у випадку механізованого наплавлення, при якій деталі в процесі наплавлення надається рівномірне обертання.
Для відновлення і підвищення терміну служби ріжучого, штампового і вимірювального інструмента, а також деталей механізмів, що працюють при інтенсивному зносі, застосовується наплавлення робочих поверхонь твердими сплавами, що представляють собою з'єднання таких металів, як титан, вольфрам, тантал, марганець, хром і інших з бором , вуглецем, кобальтом, залізом, нікелем і ін.
При виготовленні нових інструментів і деталей з твердосплавної наплавленням, як заготовок (підстав) застосовуються деталі з вуглецевих або легованих сталей. У разі ремонту деталей з великим зносом, перед наплавленням твердими сплавами роблять попередню наплавку електродами з маловуглецевої сталі.
Для отримання більш якісної наплавлення, попередження утворення тріщин і зниження напруги, в багатьох випадках доцільний підігрів заготовок до температури 300 ° C і вище.
Наплавлення металорізального інструменту та штампів. Металорізальні інструменти і штампи, що працюють при холодної та гарячої штампування, наплавляют електродами ОЗИ-3, ОЗИ-5, ОЗИ-6, ЦС-1, ЦІ-1М і інші марки. Метал, наплавлений цими електродами, має високу опірність до стирання і зминання при великих питомих навантаженнях і високих температурах - до 650-850 ° C. Твердість наплавленого шару без термообробки становить від 52 HRC (ОЗИ-5) до 61 HRC (ОЗИ-3). Наплавляється 1-3 шари загальною товщиною 2-6 мм. Деталь перед наплавленням підігрівають до температури 300-700 ° С (в залежності від марки електрода).
Наплавлення деталей, що працюють на стирання без ударних навантажень. Якщо потрібно отримати наплавлений метал особливо високої твердості, можна використовувати електроди для наплавки Т-590 і Т-620. Вони спеціально призначені для покриття деталей, що працюють на інтенсивне стирання. Їх стрижень виготовлений з маловуглецевої сталі, зате в покриття входять ферохром, ферротитан, ферробор, карбід бору і графіт. Завдяки цим матеріалам твердість наплавленого металу може досягати 62-64 одиниць по HRC.
Через те, що наплавлений метал має крихкістю і схильністю до утворення тріщин, вироби, наплавлені електродами Т-590 і Т-620, не призначені для експлуатації в умовах значних ударних навантажень. Наплавлення твердосплавного металу проводиться в один-два шари. Якщо потрібно наплавляти велику товщину, нижні шари наплавляються електродами з маловуглецевої сталі і лише заключні - твердосплавними.
Наплавлення деталей, що працюють на стирання з ударними навантаженнями. Деталі з марганцевистих сталей (110М13Л і подібні до неї), що працюють в умовах інтенсивного поверхневого зносу і високих ударних навантажень (зокрема, робочі органи будівельного і землерийного устаткування), наплавляют електродами ОМГ-Н, ЦНІІН-4, ОЗН-7М, ОЗН-400М , ОЗН-300М та інші марки. При їх використанні твердість наплавляємого металу в другому шарі виходить 45-65 HRC при високих значеннях в'язкості.
Наплавлення нержавіючих сталей. Для наплавлення деталей з нержавіючих сталей застосовуються електроди ЦН-6Л, ЦН-12М-67 і інші марки. Стрижень цих електродів виготовлений з нержавіючої високолегованої дроту. Крім високої корозійної стійкості, наплавлений метал має ще і стійкість до задиранням, що дозволяє використовувати ці електроди для наплавки поверхонь ущільнювачів в арматурних виробах.
При використанні деяких електродів для наплавлення нержавіючих сталей, рекомендується проводити попередній і супутній підігрів деталі до температури 300-600 ° С і здійснювати після наплавлення термообробку.
Наплавлення міді і її сплавів. Наплавлення міді і її сплавів (бронз) може здійснюватися не тільки на мідне або бронзове підставу, але також на сталь і чавун. У цьому випадку створюються біметалічні вироби, що мають необхідні експлуатаційні якості (високу стійкість проти корозії, низький коефіцієнт тертя та інші цінні властивості, властиві міді і її сплавів) і володіють при цьому набагато більш низькою вартістю в порівнянні з деталями, виготовленими повністю з міді або її сплавів.
Алюмінієві бронзи, зокрема, що володіють високими антифрикційними властивостями, дуже добре працюють у вузлах тертя, тому їх наплавляють на черв'ячні колеса, сухарі та інші деталі, що працюють в умовах тертя.
Наплавлення деталей з технічно чистої міді може проводитися електродами "Комсомолець-100" або присадних прутків з міді або її сплавів. При наплавленні міді на мідь застосовують попередній підігрів до температури 300-500 ° С.
Наплавлений шар бажано піддавати проковке, при температурі міді вище 500 ° С.
Якщо потрібно наплавка бронзою, можна використовувати електроди ОЗБ-2М, що містять крім, що становить основу, міді також олово, марганець, нікель і залізо. Вироби, наплавлені електродами ОЗБ-2М, мають високу поверхневу зносостійкість.
Наплавлення міді і її сплавів проводиться на постійному струмі зворотної полярності в нижньому положенні.
Наплавлення в середовищі захисних газів
Поряд з наплавленням покритими електродами, в домашніх умовах можна здійснювати і наплавку в середовищі захисних газів - методом MIG / MAG (з автоматизованою подачею дроту) або TIG (вольфрамовим електродом) з присадних прутків. Для захисту можна застосовувати різні гази: аргон, вуглекислий газ, гелій, азот - в залежності від того, який наплавляється метал.При відновленні наплавленням деталей з вуглецевих сталей можна використовувати більш дешевий вуглекислий газ. З огляду на той факт, що CO 2 окисляє розплавлений метал, наплавочная дріт в цьому випадку повинна мати раскислители (марганець, кремній і ін.).
Наплавлення міді і її сплавів можна виробляти в азоті, який нейтральний по відношенню до міді.
Високолеговані, сплави на магнієвої і алюмінієвій основі наплавляються в аргоні, гелії або їх суміші.
Наплавлення неплавким вольфрамовим електродом здійснюють в аргоні і гелії. взагалі, інертні гази, Особливо, аргон, є універсальними, придатними для зварювання та наплавлення практично будь-якого металу.
Як матеріали для наплавлення полуавтоматами вуглецевих і низьколегованих сталей застосовуються зварювальні дроту суцільного перетину (Св-08ГС, Св-08Г2С, Св-12ГС), і спеціальні наплавочні (Нп-40, Нп-50, Нп-30ХГСА). Для наплавлення нержавійки застосовують дріт з нержавіючої сталі. Може здійснюватися наплавка і порошковим дротом, що дозволяє отримати наплавлений шар з особливими властивостями.
При відновленні деталей наплавленням методом MIG / MAG застосовують як і в разі MMA постійний струм зворотної полярності, що забезпечує меншу проплавление основного металу. При використанні вольфрамового електрода (Метод TIG) використовують пряму полярність, яка виключає оплавлення вольфрамового електрода. Наплавлення потрібно намагатися вести якомога більш короткою дугою - щоб уникнути розбризкування металу.
При використанні змісту даного сайту, потрібно ставити активні посилання на цей сайт, видимі користувачами і пошуковими роботами.